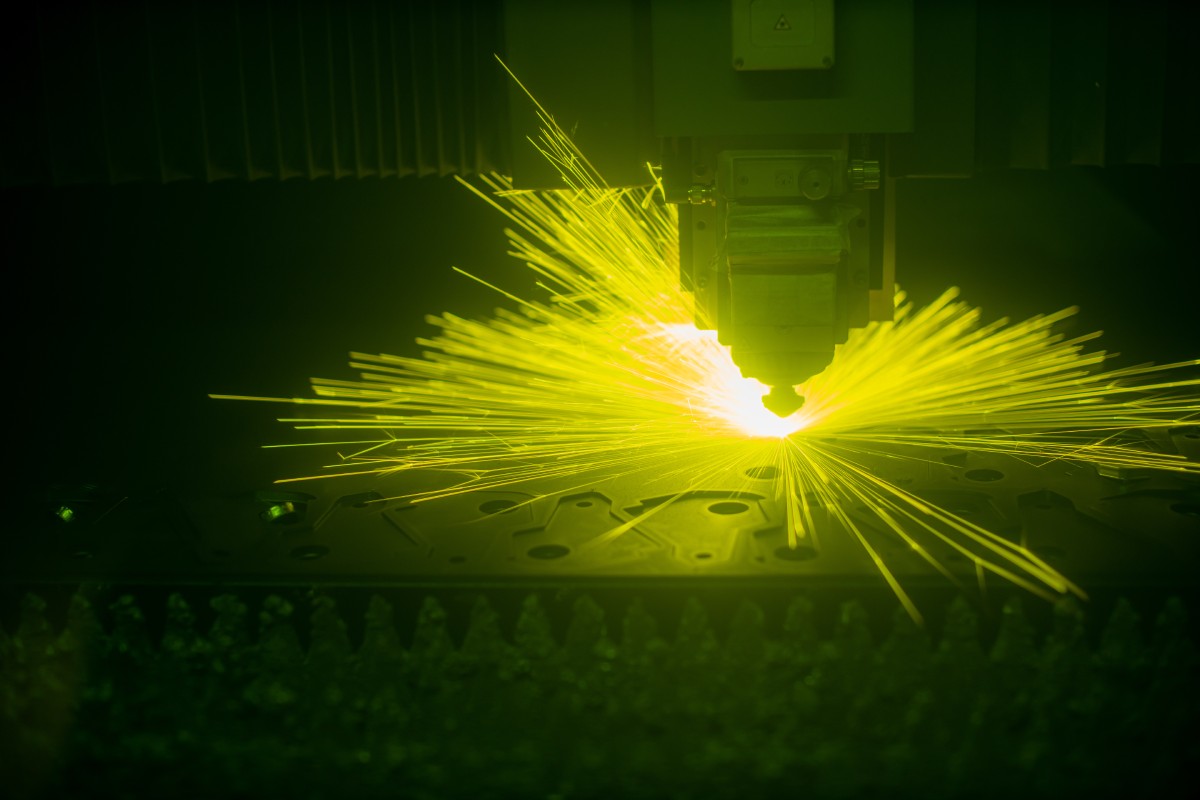
- Introduction
- Key Takeaways
- 1. How Laser Cutting Works
- 2. Preparing for Laser Cutting
- 3. The Laser Cutting Process
- 4. Post-Cutting Operations
- 5. Packaging Design
- Conclusion
- FAQs
Introduction
Laser cutting is a thermal, non-contact cutting process that uses a focused laser beam to cut through metallic and non-metallic materials with high levels of accuracy by melting or vaporizing the base material and then removing that melted material by the use of high press assist gases.
This article explores the details of the process in order to explain the limitations and some of the key considerations of the process which will also factor into part design.
Key Takeaways
- Laser cutting is a precise, non-contact cutting process that can be used on a variety of materials, including plastics, metals, and even cardboard.
- Accurate CAD files and nesting software are crucial to optimize efficiency and reduce material waste.
- Material thickness, type and laser settings determine cut quality and precision, as well as material deformation in the cutting process.
- Assist gas selection (Oxygen, Nitrogen, Compressed Air) impacts speed, quality, and efficiency.
- Post-cutting processes like deburring, grinding and tumbling are generally needed to ensure aesthetics and functionality.
1. How Laser Cutting Works
The laser beam mechanism operates by accurately directing energy to a specific area of the material. This energy is in the form of a concentrated beam of light that heats the material to a high temperature.
Depending on the material and process requirements, this heat can melt metals, burn through wood or plastics, or completely vaporize certain materials, such as thin films.
The energy is delivered with high degree of precision (±0.1mm or better is normal for cutting tolerances), and the affected area (the heat affected zone or HAZ) is generally small, while the surrounding material remains largely unaffected. This makes the process ideal for producing fine details and high-quality finishes.
The steps in the process are:
- 1. Drawing & CAM preparation
- 2. Machine Programming
- 3. Material Loading
- 4. Piercing
2. Preparing for Laser Cutting
Design File Preparation
Accurate Computer-Aided Design (CAD) files are the foundation of successful laser-cutting operations. These digital blueprints define the dimensions, shapes, and paths that the laser will follow to produce the desired parts. Precision in these files is essential; even minor inaccuracies can lead to defective cuts, material wastage, or costly rework. CAD files guide the laser cutter with exact instructions, ensuring every line and curve is executed as intended.
Among the most commonly used file formats for laser cutting are DXF (Drawing Exchange Format) and DWG (Drawing). Both formats are compatible with most laser-cutting machines and support the detailed vector information required for precise cutting paths.
DXF files, in particular, are highly favored due to their interoperability across various software and hardware platforms. Proper preparation of these files involves ensuring that all shapes are closed loops, unnecessary layers are removed, and dimensions are appropriately scaled. A clean and well-prepared CAD file minimizes errors during the cutting process and ensures seamless integration with downstream workflows.
Drawing Type | Typical File Format | Essential For | Special Considerations |
---|---|---|---|
2D | DXF | Quality Control |
|
3D | STP, STEP, and SolidWorks | Accurate Quoting | CNC bending: 3D drawings allow a manufacturer to better optimize designs for manufacturability |
Table 1: Typical Design File Formats
Nesting for Material Optimization
Nesting is the process of arranging parts within a sheet of material in a way that minimizes waste and maximizes material usage. Effective nesting is critical in laser cutting, where the cost of raw materials often constitutes a significant portion of production expenses. By optimizing how parts are laid out, manufacturers can reduce material scrap, improve cost efficiency, and enhance sustainability.
Arranging Parts To Minimize Material Waste
Advanced software tools analyze the geometry of parts and arrange them within the material boundaries to ensure minimal gaps between components. Some software even considers factors like part orientation, material grain direction, and cutting path efficiency. For example, parts with similar shapes might be rotated or mirrored to fit together snugly, much like pieces of a jigsaw puzzle.
Creating CAM Programs
CAM software converts the vector-based CAD files into G-code, a programming language that directs the movements of the laser cutting machine.
Creating effective CAM programs involves specifying critical parameters such as laser power, cutting speed, and assist gas settings based on the material type and thickness.
Operators must also consider the sequence of operations to minimize thermal distortion and ensure efficient cutting.
3. The Laser Cutting Process
Machine Programming
The laser cutting process begins with machine programming, where the CAM (Computer-Aided Manufacturing) file, which contains the cutting instructions, is loaded into the laser cutter’s control system. The operator inputs critical details, including production quantities, material type, thickness, and specific cutting parameters such as speed and power settings.
Operators also set up the machine to optimize efficiency by determining the order in which cuts are made, balancing the need for speed with the prevention of thermal distortion. For instance, cuts are often sequenced to distribute heat evenly across the material, avoiding warping.
Material Loading
The raw material, typically in the form of flat sheets, is loaded onto the laser cutting bed. This can be done manually or with the aid of automated systems such as material towers, cranes, or forklifts. Automated loading systems are particularly advantageous in high-volume production environments.
Ensuring the material is correctly aligned on the cutting bed is critical. Misaligned sheets can lead to inaccurate cuts, wasted material, and potential damage to the machine.
Piercing Process
Before the laser can follow its cutting path, it must first pierce the material to create an entry point. This piercing process involves concentrating the laser’s energy on a single spot until the material melts or vaporizes, forming a hole.
Piercing is the most time-intensive phase of laser cutting because it requires a high level of energy and precision. Assist gases such as oxygen, nitrogen, or air, play a crucial role in this stage.
Removing Vaporized or Melted Materials
As the cutting process continues, the material is removed by blowing away this material from the cutting path. This gas is introduced in a continuous method to create a kerf. They also play a role in cooling, protecting the optics of the laser, and influencing the chemical interactions during cutting.
Cutting Process
The laser follows the pre-programmed path to cut the material. Once the piercing is complete, the laser transitions to continuous cutting, following the programmed path to produce the desired shape.
Generally, it is the laser beam which is moving via a CNC-controlled gantry, rather than the workpiece or material being moved, but this depends on the type of laser cutter. For tube cutting and some other processes, it is the part which is moved while the laser is fixed.
4. Post-Cutting Operations
Unloading and Part Separation
Once the laser-cutting process is complete, the finished parts must be carefully unloaded from the cutting bed. This involves removing both the usable components and the leftover skeleton material. Depending on the complexity and volume of the operation, this step can be performed manually or with automated systems, such as robotic arms or conveyor systems, to ensure efficiency and safety.
Deburring and Finishing
After parts are removed from the cutting bed, they may require deburring and finishing to ensure smooth edges and a polished appearance. Laser cutting often leaves minor imperfections, such as burrs or sharp edges, particularly when cutting thicker materials or intricate designs.
Deburring involves removing these imperfections, typically using manual tools, power tools, or automated deburring machines. Techniques vary based on material and part design:
- Grinding or Polishing: For a finer finish, especially on parts visible in the final product, grinding or polishing is used to create a smooth and uniform surface. These methods also help remove any oxidation or discoloration that may occur during cutting.
- Automated Deburring: units are loaded onto a flat bed which runs through a deburring machine; this machines essentially uses large abrasive brushes or other tools to ensure all edges are smooth and any burrs remove. They can also achieve a brushed appearance at the same time.
Finishing processes are particularly critical for components intended for industries with high aesthetic or functional demands, such as automotive, aerospace, or consumer electronics.
Factors Impacting the Laser Cutting Process
Laser Cutting Speed
The laser moves at varying speeds depending on factors such as material thickness, complexity of the design, and the material’s properties.
- Straight lines are cut quickly, while sharp curves and intricate details require slower speeds to maintain accuracy.
- Material thickness significantly influences the cutting speed; thicker materials require more energy and slower cuts to ensure the laser penetrates fully.
- Reflective materials, such as copper and brass, present additional challenges due to their tendency to reflect laser energy, requiring specialized lasers or coatings.
- For non-metal materials like plastics or wood, the laser’s power must be carefully controlled to prevent excessive heat, which can cause charring or deformation.
Factors Affecting the Quality of the Cut
Cutting quality in laser processes is determined by the interplay of several factors, with material type, laser power, and cutting speed being the most critical.
Material Type
The physical and chemical properties of the material being cut significantly impact the laser cutting outcome.
- Metals such as steel and aluminum are commonly used due to their predictable behavior under high heat and their compatibility with assist gases.
- Reflective metals like copper and brass, however, pose challenges because they tend to reflect the laser beam, reducing its efficiency.
- Non-metallic materials, such as plastics and wood, behave differently and require customized settings to prevent heat damage or warping.
Laser Power
The power of the laser beam determines how effectively it can cut through a material.
- Higher power is required for thicker or denser materials to ensure full penetration.
- Thinner or less dense materials can be processed with lower power to avoid overcutting or burning.
- For example, cutting stainless steel may require a power setting of 1000 watts or more, while thin acrylic sheets can be cleanly cut at a fraction of that power.
Cutting Speed
- The speed at which the laser moves over the material plays a crucial role in cutting quality.
- Faster speeds are suitable for straight cuts on thin materials, as they reduce heat input and prevent unnecessary energy loss.
- Intricate designs, sharp radii, or thicker materials demand slower speeds to maintain precision and ensure complete penetration.
Role of Assist Gases (Oxygen, Nitrogen, Air) in the Process
Assist gases are fundamental to laser cutting processes, significantly influencing the speed, quality, and efficiency of the operation. These gases not only serve to blow away molten material from the cutting path but also play roles in cooling, protecting the optics of the laser, and influencing the chemical interactions during cutting. Their selection is critical and depends on the material type, desired edge quality, and production cost considerations.
Oxygen
- Primarily used for cutting mild steel and thick metals.
- Creates an exothermic reaction with hot metal, increasing local heat intensity for faster cutting speeds.
- Challenges include oxidized or burnt edges, often requiring additional cleaning or finishing.
Nitrogen
- Ideal for cutting stainless steel, aluminum, and other non-ferrous metals.
- Acts as an inert shield to prevent oxidation, producing clean, smooth, and discoloration-free edges.
- Requires higher laser power and slower cutting for thicker materials but delivers precise, pristine edge finishes.
- Commonly used for high-end components or decorative metalwork where aesthetics are critical.
Compressed Air
- A versatile, cost-effective option for cutting non-metallic materials and less demanding applications.
- Contains a mix of oxygen and nitrogen, offering moderate cutting performance at a lower cost.
- Suitable for plastics, wood, and other non-metals where edge discoloration is not a concern.
Other Notes
Reflective Materials
Reflective materials like copper and brass are quite difficult to cut using conventional lasers.
- These materials can reflect a significant portion of the laser’s energy, reducing its effectiveness and risking potential damage to the machine’s optics.
- Specialized lasers, such as fiber lasers or lasers with anti-reflective coatings, are often employed to overcome these challenges.
- In some cases, pre-treating the surface of reflective materials with a coating can also improve cutting efficiency.
Plastics and Wood
Cutting plastics and wood requires lower laser power and precise heat control to prevent unwanted effects like charring, melting, or burning.
- Plastics such as acrylics tend to melt if exposed to excessive heat, leaving rough or uneven edges.
- Wood, is prone to burning, resulting in discoloration or charred edges.
Quality Control
The final step in post-cutting operations is quality control. Generally, parts are sampled at the start of production (First Article Inspection, or FAI), and lot sampling is conducted during production according to AQL requirements.
Measurements are taken to ensure the parts conform to the original design specifications and tolerances. In high-precision industries, such as aeronautics, may require 100% inspection of all parts as even minor deviations can compromise functionality or safety.
Quality control may involve:
- Visual Inspections: To identify surface imperfections, scratches, or discolorations.
- Dimensional Checks: Using calipers or 2D projection devices is usually sufficient to ensure laser cut part dimensional quality.
- Surface Finishing Testing: parts which are finished with powder coating, anodization or other finishes, will often undergo gloss testing, thickness checks, surface roughness evaluation, color checks or other evaluation to ensure finish quality and consistency.
5. Packaging Design
Finished laser-cut parts, whether delicate, heavy or intricately designed, require robust and secure packaging to prevent damage during handling and transportation.
- For example, sharp-edged metal parts are often wrapped in protective materials such as foam, bubble wrap, or corrosion-resistant paper to safeguard against both physical and environmental damage.
- Components requiring high precision or with fragile finishes, such as polished metal or painted surfaces, demand careful handling
- Specialized crates, shock-absorbent padding, and secure strapping mechanisms are often used to minimize vibrations or movement during transit.
Conclusion
Laser cutting stands as one of the most efficient and versatile manufacturing processes, offering unparalleled precision and adaptability across a wide range of materials. From understanding the principles of laser operation to ensuring high-quality post-cutting finishes, each stage of the process plays a crucial role in delivering parts that meet exacting standards. Proper planning, careful execution, and meticulous attention to detail ensure that laser cutting not only meets but exceeds industry expectations, making it a cornerstone of modern manufacturing.
FAQs
What is the role of assist gases in laser cutting, and how do they influence cut quality?
Assist gases such as oxygen, nitrogen, and compressed air impact cutting speed, edge quality, and the thermal characteristics of the cut. Oxygen supports faster cutting through exothermic reactions, nitrogen prevents oxidation for clean edges, and compressed air offers a cost-effective solution for non-metals.
How does material thickness affect the choice of laser power settings?
Thicker materials require higher laser power to ensure complete penetration, while thinner materials need lower power to avoid overburning or distortion. Precision adjustments depend on the material type and cut geometry.
What are the challenges of cutting reflective materials like copper and brass?
Reflective materials tend to redirect a portion of the laser’s energy, reducing cutting efficiency and posing a risk to the machine’s optics. Fiber lasers or anti-reflective coatings are typically used to overcome these challenges.
How does nesting optimize material utilization in laser cutting?
Nesting arranges parts on a material sheet to minimize gaps and reduce waste. Advanced software tools analyze geometry and consider factors such as orientation, grain direction, and cutting path efficiency to maximize material usage.
Why are CAD files critical in laser cutting, and what features must they include?
CAD files serve as the blueprint for laser cutting, defining dimensions, shapes, and cutting paths. Files must include closed loops, appropriate scaling, and removal of unnecessary layers to ensure accuracy and seamless machine operation.
How does the piercing process differ from the cutting process in laser operations?
Piercing requires concentrated laser energy to create an entry point, often involving more time and precision than continuous cutting. Assist gases play a crucial role in clearing molten material during piercing.
What are the factors that influence cutting speed in laser processes?
Cutting speed is affected by material thickness, design complexity, and material properties. Straight cuts on thin materials allow faster speeds, while intricate shapes or thicker materials require slower speeds for precision.
How does thermal distortion affect the laser-cutting process, and how is it minimized?
Thermal distortion can warp materials due to localized heating. To minimize it, operators sequence cuts to distribute heat evenly and optimize cutting parameters like speed and assist gas usage.
What are the key quality control measures for laser-cut parts?
Quality control includes dimensional checks, surface inspections, and testing for finish consistency. Techniques like visual inspection, calipers, or gloss testing ensure that parts meet design specifications and functional requirements.
Why is deburring necessary after laser cutting, and what methods are used?
Deburring removes imperfections such as sharp edges and burrs left during cutting. Common methods include grinding, polishing, and automated deburring machines, depending on the material and required finish.
How does material alignment on the cutting bed impact laser cutting accuracy?
Misaligned materials can result in inaccurate cuts, wasted material, and potential machine damage. Proper alignment ensures that the laser follows the programmed path precisely, reducing errors.