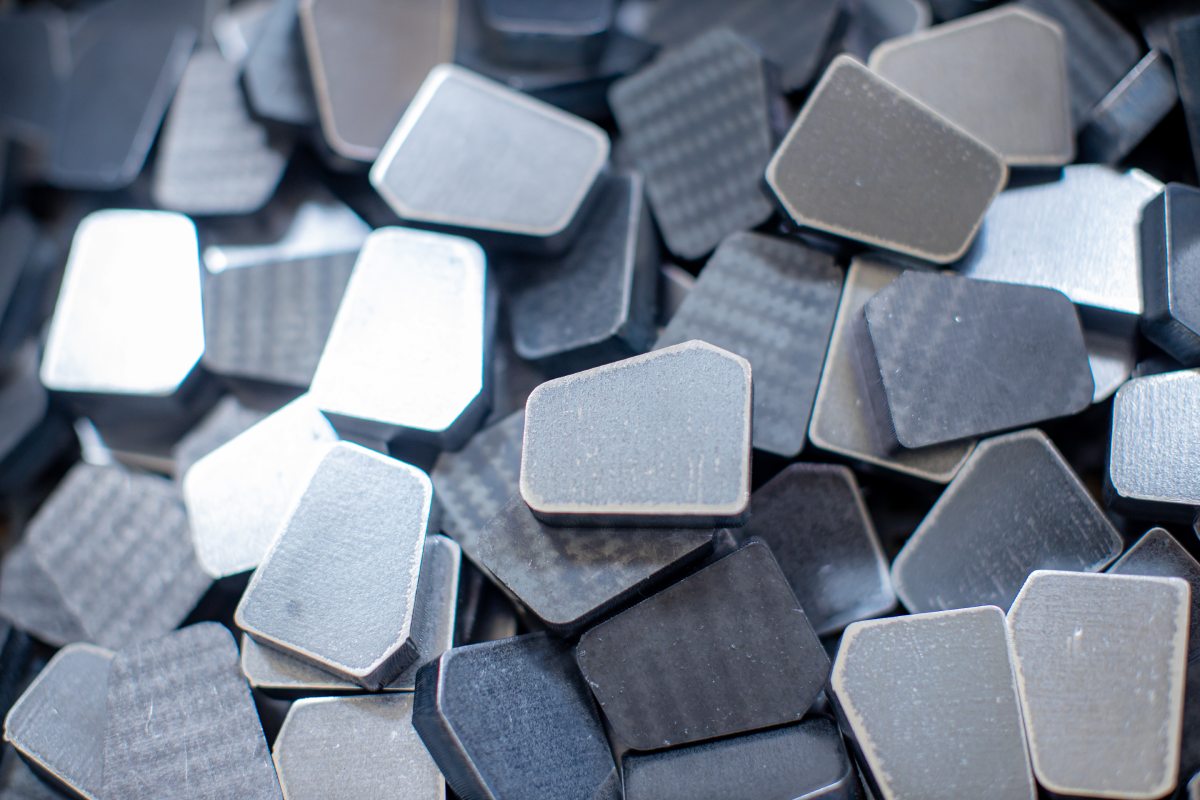
- Introduction
- Factors Influencing Laser Cutting & Part Costs
- Additional Cost Considerations in Laser Cutting
- How to Reduce Laser Cutting Part Costs
- Shipping and Handling Costs
- Conclusion
- FAQs
Introduction
Several factors influence the cost of laser-cutting parts such as the type of material being cut, its thickness, and the complexity of the part design. The total quantity of parts ordered is an important factor as larger production runs benefit from economies of scale, reducing the per-unit cost. This article will provide you with various options and suggest suitable material to reduce your laser cut part.
Fig. 1: Laser Cutting Process
Factors Influencing Laser Cutting & Part Costs
Material Type
The material of the part directly impacts the process's efficiency and cost. Different materials such come with unique cutting requirements that influence the energy consumption, cutting speed, and thereby the overall cost of the part.
Quantity and Batch Size
The per unit cost is greatly influenced by quantity and batch size through economies of scale. Larger orders spread setup costs—like machine programming, calibration, and material handling—over more units, reducing the per-unit cost.
For example, a $500 setup cost divided by 50 units results in a $10 per unit cost. For the same part, but with 500 units, it drops to $1 per unit.
Continuous machine operation with larger batches decreases downtime and increases efficiency. Ordering larger quantities reduces the overall price per unit by efficiently distributing the set up and engineering costs for part production.
Cutting Time
Cutting time is a critical factor in laser cutting, directly influencing the overall cost of the process. Two primary aspects—material thickness and the number of holes or cutouts—significantly affect the cutting time and, consequently, the price.
Material Thickness
The thickness of the material being cut significantly impacts the cutting time due to several factors. Thicker materials require higher laser power to effectively penetrate and cut through, leading to increased energy consumption and higher operational costs.
To ensure a clean and precise cut, the cutting speed must be reduced, which prolongs the time the laser spends on each part and extends the overall cutting time.
Thicker materials dissipate heat less efficiently, necessitating additional passes or even slower speeds to prevent damage, further increasing the cutting duration. Consequently, as the material thickness rises, so do the associated costs, including energy usage, machine wear, and labor expenses.
Thicker material will often require additional post processing after cutting, as laser cutting will tend to leave rougher edges on the parts thicker than 10mm that may need deburring, tumbling or sanding.
Number of Holes and Cutouts
The number of holes or cutouts in a design also significantly impacts cutting time:
- Pierce Points: Each hole or cutout requires the laser to pierce the material, initiating a cut. These pierce points are time-consuming as the laser needs to focus additional energy to start each new cut. More pierce points mean more time is spent initiating cuts rather than moving along a continuous path.
- Complexity and Path Length: A higher number of cutouts increases the complexity and length of the cutting path. The laser must follow intricate patterns, which slows down the overall cutting process. This increased complexity requires more time and precision, further extending the cutting duration.
- Precision and Quality: Ensuring that each hole or cutout meets precise specifications may necessitate slower cutting speeds and additional passes, especially for intricate or small features. This additional precision work adds to the total cutting time.
Part Handling
Loading and unloading materials for laser cutting involves significant manual labor, requiring skilled workers to correctly position and secure raw material sheets, impacting labor costs, especially for large or heavy sheets that may need additional equipment like forklifts or hoists.
Some facilities invest in automated material handling systems to reduce these costs and increase efficiency, though the initial investment is high.
Post-cutting, parts need to be carefully separated from the sheet, a labor-intensive process that can be costly, particularly for intricate designs.
Fig. 2: Specifications View of a Sheet Metal Part In Komacut Application
Additional Cost Considerations in Laser Cutting
Surface finishing
Surface finishing is a crucial aspect of laser cutting that significantly impacts production costs due to various post-processing steps needed to meet aesthetic or functional requirements.
- Deburring removes sharp edges and burrs, with manual deburring being labor-intensive and costly, while automated machines require an initial investment but lower long-term labor expenses.
- Polishing enhances surface smoothness and appearance, adding to material and labor costs.
- Grinding provides a uniform surface finish and removes residual slag, involving costs for machines, abrasive materials, and skilled operators.
- Powder coating protects the metal from corrosion and enhance aesthetics, with costs including materials and labor, especially for processes requiring multiple layers or specific curing.
- Anodizing and plating improve surface hardness and resistance, with higher costs due to the chemicals and precise control required. Each surface finishing type, whether manual or automated, adds distinct costs related to labor, materials, and equipment.
Chamfering
Chamfering involves beveling the edges of a part for improved fit and aesthetics, typically requires precise machining, increasing both time and expense.
Thread Holes
These necessitate accurate fixturing, drilling and tapping, often performed manually or with specialized machinery. They need to be processed one by one, which results in relatively high cost per hole versus through holes produced by laser cutting.
Fig. 3: Surface Finished Sheet Metal Parts
How to Reduce Laser Cutting Part Costs
Optimizing Design for Manufacturing
To reduce laser cutting costs, optimizing the Design For Manufacturing (DFM) is crucial. Simplifying designs can significantly lower costs without compromising functionality. Here are some tips:
- Minimize Complex Geometries: Reduce the complexity of the design by avoiding intricate patterns and tight tolerances to decrease cutting time. Simplified shapes require less precise laser control, which translates to faster cutting speeds and lower costs.
- Reduce the Number of Cutouts: Designs with fewer holes or cutouts minimize the number of pierce points and reduce the overall cutting path length. This not only reduces the laser operation time but also decreases material handling and finishing efforts.
- Standardize Part Sizes: Use standard sizes for parts allowing better nesting, which maximizes material usage and reduces waste. Efficient nesting can result in significant material cost savings.
- Design for Efficient Nesting: Arrange parts in a way that maximizes the use of the material sheet. Utilizing nesting software can help in creating layouts that minimize scrap and optimize the cutting path.
- Combine Multiple Parts: Where possible, combine multiple small parts into a single larger cut. This reduces the number of individual cuts and handling steps required.
Bulk Ordering
Bulk ordering in laser cutting effectively reduces per-unit costs by leveraging economies of scale, where larger orders spread fixed setup costs over more units, thus lowering the cost per unit. It also benefits from bulk material discounts, as suppliers often provide better rates for larger orders, reducing raw material costs.
Material Selection
Choose cost-effective materials that meet project requirements to reduce laser-cutting costs. Here’s how to make smart material choices:
- Consider Material Properties: Select materials that are easier and faster to cut. For example, thinner or softer materials generally require less laser power and cutting time, reducing energy and operational costs.
- Evaluate Material Costs: Compare the cost of different materials that can achieve the same functional requirements. Opt for materials that provide the necessary performance characteristics at a lower cost.
- Balance Quality and Cost: While lower-cost materials can reduce expenses, it’s important to ensure they meet the required quality and durability standards. Poor-quality materials can lead to higher reject rates and additional post-processing costs.
- Leverage Supplier Relationships: Building strong relationships with material suppliers can lead to better pricing, priority access to materials, and more favorable terms, contributing to overall cost savings.
- Utilize Material Substitutes: In some cases, material substitutes can provide significant cost savings. For instance, using coated carbon steel instead of stainless steel can offer similar corrosion resistance at a lower cost.
Fig. 4: Order Quantity vs Price per Unit
Shipping and Handling Costs
Shipping and handling costs significantly influence the final price of laser-cut parts, with factors such as distance and delivery options playing crucial roles. Longer shipping distances typically incur higher costs due to increased fuel consumption, transportation time, and potential customs fees for international deliveries.
Conclusion
Reducing laser-cutting costs involves a multifaceted approach, focusing on key factors that drive expenses. We explored the importance of material type, where different materials have unique cutting requirements that affect costs. Efficient nesting can significantly lower material waste and cutting time, leading to substantial savings. Ordering larger quantities takes advantage of economies of scale, reducing the price per unit by spreading setup costs over more units. Cutting time is influenced by material thickness and the number of holes or cutouts, both of which increase costs with increased complexity and time. Labor costs extend beyond setup to include loading, unloading, and separating parts, all of which add to the total expense.
To manage and reduce costs, optimize your design for manufacturing, order in bulk, and select the material carefully. Simplifying designs, reducing the number of cutouts, and ensuring efficient nesting can lower production costs without sacrificing functionality.
FAQs
What factors most influence the cost of laser cutting?
The primary factors affecting laser cutting costs include material type, thickness, design complexity, cutting time, labor costs, and finishing processes. Each of these elements contributes to the overall expense by impacting the efficiency and resources required for the cutting process.
How does material thickness impact laser cutting costs?
Thicker materials require more energy and slower cutting speeds to achieve a clean cut. This increases the cutting time and energy consumption, leading to higher overall costs. Additionally, thicker materials may necessitate more frequent maintenance of cutting equipment due to increased wear and tear.
Why does the number of cutouts affect the cost?
The number of cutouts affects the cost because each cutout requires a pierce point where the laser initiates the cut. More pierce points and a longer cutting path increase the cutting time and energy required, which raises the overall cost. Intricate designs with numerous cutouts also demand greater precision, adding to labor and equipment expenses.
How can I reduce the cost of laser cutting?
To reduce laser cutting costs, you can optimize your design for manufacturing by simplifying geometries, reducing the number of cutouts, and ensuring efficient nesting. Ordering in bulk can spread setup costs over more units, and choosing cost-effective materials that meet your project requirements can also lower expenses. Efficient process management and automation can further reduce labor costs.
What is the role of nesting in reducing costs?
Efficient nesting maximizes material usage by arranging parts closely together on the material sheet, minimizing waste. This reduces the amount of raw material needed and decreases cutting time, leading to significant cost savings. Advanced nesting software can help optimize layouts, enhancing efficiency and reducing scrap.
Does bulk ordering significantly reduce the per-unit cost?
Yes, bulk ordering can significantly reduce the per-unit cost by spreading fixed setup costs over a larger number of units. Additionally, bulk orders often qualify for material discounts from suppliers, further lowering the overall cost. Larger batch sizes also improve production efficiency, reducing machine downtime and labor costs.
How do secondary processes like chamfering and threading impact costs?
Secondary processes such as chamfering and threading add to the overall cost by requiring additional labor, specialized equipment, and extended production time. These processes are necessary for parts that need specific mechanical features or high-quality finishes, but they increase the complexity and duration of the manufacturing cycle, thus raising costs.
Are there cost differences between cutting different materials?
Yes, different materials have unique properties that affect cutting speed, energy consumption, and equipment wear. For example, cutting stainless steel generally requires more energy and time compared to cutting carbon steel, making it more expensive. Soft or thin materials, on the other hand, are typically faster and cheaper to cut.
Can surface finishing affect the total cost of laser cutting?
Yes, surface finishing processes such as deburring, polishing, grinding, and coating add to labor and material costs. These additional steps are essential for achieving the desired surface quality and meeting specific aesthetic or functional requirements, but they increase the overall expense due to the time and resources involved.