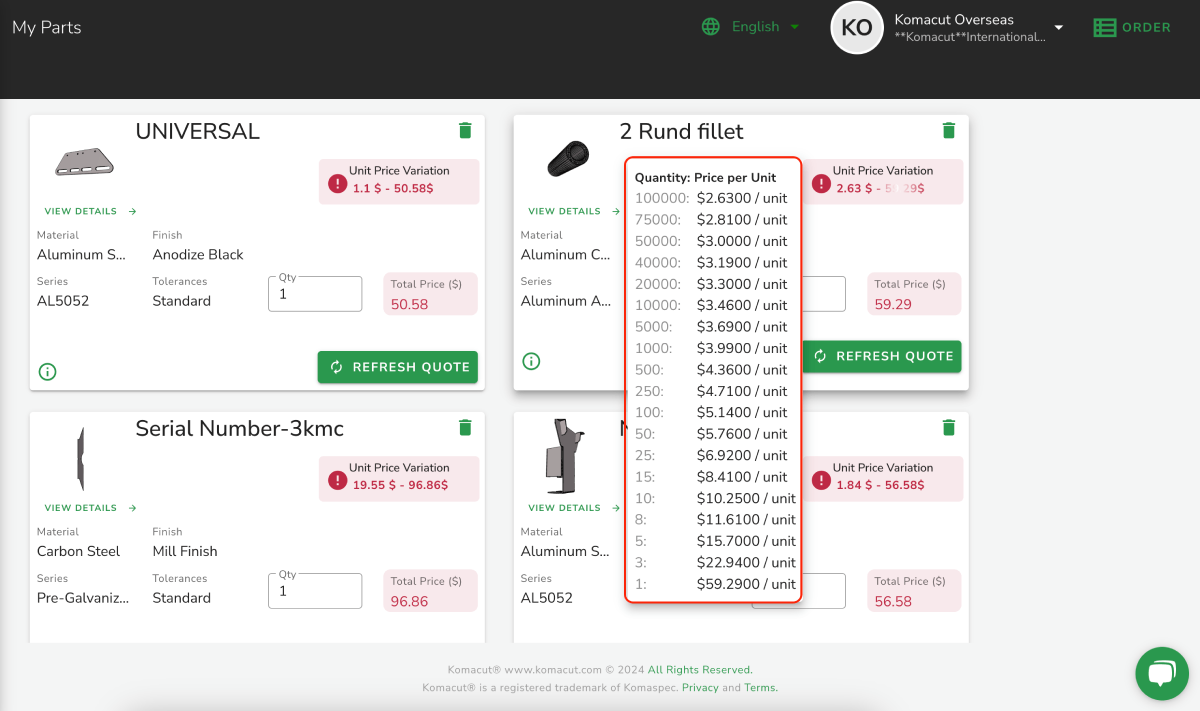
- Key Takeaways
- Factors Influencing CNC Machining Costs
- Additional Cost Considerations in CNC Machining
- How to Reduce CNC Machining Costs
- Conclusion
The cost of CNC machined parts can vary significantly depending on several key factors. If you want to reduce your cost of CNC machined parts then this article will help you in planning and budgeting for CNC machining projects effectively.
These factors are ranked in rough priority from most to least impactful on cost, although specific circumstances can alter their relative importance. Understanding these elements helps anticipate the financial commitment involved in CNC machining services and parts production:
- Batch Size - Typically, the larger the quantity of parts ordered, the lower the cost per unit. This is due to the spread of setup costs over a larger number of parts, achieving economies of scale.
- Material Type - Different materials have different costs, influenced by their availability and the difficulty involved in machining them. For example, metals like titanium are generally more expensive than softer materials like aluminum.
- Material Usage - The amount of material required and the waste produced during machining also affect costs. Efficient use of materials can reduce overall expenses.
- Machining Time - The complexity of the part design affects how long it takes to machine each part. More complex parts require longer machining times, increasing the cost.
- Post-Processing - Any additional finishing required after the initial machining, such as polishing, anodizing, or painting, will add to the cost.
Key Takeaways
Managing costs in CNC machining requires a deep understanding of several key factors that directly influence the overall expenses of production. Here are the key strategies for cost reduction:
- Optimize part manufacturability by simplifying geometry and reducing radii, blind holes or other features to reduce the number of machine setups.
- Apply tight tolerances only where absolutely necessary to minimize cost
- Choose materials that are faster and easier to machine and handle
- Increase batch size where possible; ordering 100 pieces in one go is much cheaper than 5 batches of 20 pieces
- Minimize the need for secondary operations, such as fining or surface finishing, to save on labor and handling costs
- No Sharp Radii or Corners
- Avoid sharp, 90-degree internal corners, as these require the machine to stop and reposition the part, increasing machining time and expenses.
- Instead, using rounded internal corners allows the machine to run continuously, lowering production costs.
- Ideally, design with an inside corner radius that maintains a length-to-diameter (L) ratio of 3:1 or less and keep internal corner radii consistent whenever possible to further optimize efficiency.
- No Blind Holes
- Parts with deep internal pockets require extensive material removal, additional time, and special tools.
- Aim to limit pocket depths to four times their length, ideally two to three times the tool's diameter, to stay within the cutting limits of CNC tools.
- As a best practice, design parts with a length-to-depth ratio of up to 4:1, as deeper pockets become exponentially more expensive to produce.
- Reduce Thread Length
- Optimize the length of threads by avoiding unnecessarily long threads
- Increasing thread length beyond three times the hole's diameter requires special tools and adds time, increasing costs expenses.
- Generally, very long threads only marginally increase fastener hold, but greatly increase machining time and cost
- Use Standard Holes & Threads
- Use standard drill sizes for holes, as non-standard sizes often require end mill tools, increasing expenses.
- Reduce Hole Depth
- The depth of holes also affects cost; while holes up to ten times the diameter can be machined, they are more challenging and costly.
- For holes with diameters up to 10 millimeters, design in 0.1-millimeter increments; for diameters above 10 millimeters, use 0.5-millimeter increments.
- Try to keep the hole length to no more than four times its diameter to optimize cost.
- Small Features Equal Higher Cost
- Parts with small features with a high width-to-height aspect ratio are difficult to machine accurately and increase expenses.
- Keep all features with a width-to-height ratio below four, and improve their stiffness by connecting them to thicker walls or reinforcing them with bracing support ribs on all four sides.
- Avoid Thin Walls
- Re-consider designing parts with thin walls, as they are fragile, prone to distortion, and difficult to maintain tolerances, leading to increased expenses.
- Thicker walls provide greater stability and are more cost-effective to machine.
- If weight is not a critical factor, design metal parts with walls thicker than 0.8 millimeters and plastic parts with walls thicker than 1.5 millimeters.
Factors Influencing CNC Machining Costs
Material Type & Usage
The selection of materials for CNC machining projects significantly impacts the overall cost. This impact is due to several factors including the cost of raw materials, their machinability, and the physical properties required for the final product.
Overview of Common Materials Used in CNC Machining
CNC machines can handle a wide range of materials, each offering different benefits and challenges:
- Metals - Commonly used metals include aluminum, stainless steel, and titanium. These materials are chosen for their strength, durability, and resistance to corrosion and heat. For example, aluminum is lightweight and easy to machine, making it ideal for automotive and aerospace applications.
- Plastics - Plastics like ABS, polycarbonate, and PEEK are popular due to their lighter weight, corrosion resistance, and varying degrees of heat resistance. They are commonly used in consumer electronics, automotive components, and even medical devices.
- Composites - These materials, such as carbon fiber-reinforced polymers, offer high strength-to-weight ratios and are used in specialized applications like aerospace and sporting goods.
Plastic Materials | Type | Approximate Cost (RMB) | Approximate Cost (USD) |
---|---|---|---|
ABS | Acrylonitrile Butadiene Styrene | ¥20.00 | $2.80 |
ABS V0 | Fire Retardant ABS | ¥23.00 | $3.25 |
PE | Polyethylene | ¥14.00 | $2.00 |
HDPE | High-Density Polyethylene | ¥12.00 | $1.70 |
PC | Polycarbonate | ¥30.00 | $4.20 |
ABS + PC | ABS and Polycarbonate Blend | ¥28.00 | $3.90 |
POM | Polyoxymethylene | ¥35.00 | $4.90 |
PMMA | Polymethyl Methacrylate (Acrylic) | ¥22.00 | $3.10 |
TPE | Thermoplastic Elastomer | ¥40.00 | $5.60 |
PP | Polypropylene | ¥15.00 | $2.10 |
PA | Polyamide (Nylon) | ¥33.00 | $4.65 |
PA66 | Polyamide 66 (Nylon 66) | ¥36.00 | $5.10 |
PA + 15% | Polyamide with 15% Glass Fiber | ¥32.00 | $4.50 |
PA + 30% | Polyamide with 30% Glass Fiber | ¥32.00 | $4.55 |
Table 1: Approximate Cost per Kilogram of Common CNC Plastic Materials
Cost Differences Between Materials
The cost of materials can vary widely:
- Carbon Steels - these are the most cost effective and common alloys used for parts, and the material cost is generally 1/3 or less of stainless or aluminum. The downside is that these alloys are prone to corrosion, need additional surface finishing and have in general worse physical properties (lower strength, etc.)
- Stainless Steel vs. Aluminum - Stainless steel is generally more expensive than aluminum due to its superior strength and heat resistance properties. However, aluminum's easier machinability and lighter weight can reduce overall machining costs, even if material cost per kilogram is similar.
- Titanium - Known for its high strength and corrosion resistance, titanium is significantly more expensive than many other metals. It is often reserved for critical applications in aerospace and medical devices where its properties are indispensable.
Metal Materials | Type | Approximate Cost (RMB) | Approximate Cost (USD) |
---|---|---|---|
SPCC | Cold Rolled Steel | ¥5.25 | $0.75 |
SGCC | Galvanized Steel | ¥6.52 | $0.90 |
SAPH440 | Hot Rolled Steel | ¥5.10 | $0.75 |
Q235 | Carbon Steel | ¥4.80 | $0.70 |
Q345 | Low Alloy Steel | ¥5.40 | $0.80 |
Spring Steel-65Mn | Spring Steel | ¥9.00 | $1.25 |
AL5052 H32 | Aluminum Alloy | ¥20.00 | $2.80 |
AL6061 T6 | Aluminum Alloy | ¥23.00 | $3.20 |
SS301 | Stainless Steel | ¥18.00 | $2.50 |
SS304 | Stainless Steel | ¥21.00 | $3.00 |
SS316 | Stainless Steel | ¥24.00 | $2.40 |
Table 2: Approximate Cost per Kilogram of Common CNC Metal Materials
Impact of Material Choice on Overall Cost
The choice of material significantly impacts both the cost and the machining process in CNC manufacturing. Materials like stainless steel and titanium, which are harder and tougher, require more time and specialized tooling, thereby increasing costs.
Conversely, softer materials such as aluminum are easier to machine, which can reduce both machining time and tool wear. Machinability also varies, as some materials may necessitate specific CNC machines or unique settings to handle characteristics like melting points, as seen with plastics.
Quantity and Batch Size
The cost of CNC machined parts is heavily influenced by the quantity ordered, benefiting from economies of scale where larger quantities spread fixed setup costs, like equipment preparation and programming, across more units, thus reducing the cost per part.
Bulk material purchases also often attract discounts, further lowering expenses. Strategic decision-making is crucial when choosing between low and high-volume production; low-volume may be preferable for prototypes requiring specific customization despite higher per-unit costs, while high-volume production efficiently reduces costs per part by amortizing initial investments over a larger output, ideal for standardized items with steady demand.
Fig. 1: Komacut's Sheet Metal Quotation Platform
Machining Time
Machining time is a critical factor in determining the cost of CNC machined parts. The duration it takes to machine a part directly impacts labor costs and machine operation costs. Two significant elements that influence machining time are the thickness of the materials being used and the complexity of the part's design.
Impact of Material Thickness
The thickness and hardness of the material significantly impact the machining time and cost of CNC operations. Thicker materials necessitate multiple passes of the cutting tool to achieve the required depth with precision, increasing both the direct machining time and the wear on tools, which can lead to higher maintenance costs. Similarly, harder materials require slower feed rates to prevent damage to both the cutting tool and the part being machined, further extending the machining time and consequently raising production costs.
Complexity of Design
The complexity of a part's design directly impacts CNC machining time and costs due to the need for intricate detailing and precise control. Complex designs that include features like holes, cutouts, fine details, and tight tolerances require slower machining speeds to ensure accuracy, increasing both machining time and the likelihood of frequent tool changes or the need for specialized tools.
Additionally, such parts often necessitate more sophisticated setups or custom fixtures to accommodate their unique geometries, and the programming for these designs is more involved and time-consuming, demanding a higher skill level from programmers.
Type & Complexity of Machining
CNC Milling – 3 vs 4 vs 5 Axis
CNC milling machines use rotary cutters to remove material from a workpiece by advancing (or feeding) in a direction at an angle with the axis of the tool. The complexity and capability of CNC milling vary significantly based on the number of axes.
- 3-Axis Milling - This is the simplest form of CNC milling and involves three axes of motion: horizontal, vertical, and depth (X, Y, and Z). 3-axis milling is sufficient for many operations and is typically the least expensive option, suitable for parts with relatively simple geometries.
- 4-Axis Milling - Adds the ability to rotate the workpiece, known as the A-axis, allowing for more complex shapes and features to be machined, including those that are not parallel or perpendicular to any of the primary three axes. This capability increases the types of operations that can be performed in a single setup, reducing the need for repositioning and thus can enhance both accuracy and productivity.
- 5-Axis Milling - This type of machine provides the highest level of precision and flexibility. It adds a second rotational axis, the B-axis, enabling the tool to approach the workpiece from almost any direction. 5-axis machines can produce highly complex and intricate parts with fewer setups and shorter machining times compared to 3-axis and 4-axis. However, these machines are also the most expensive, not only in terms of machine costs but also for operation, maintenance, and even programming.
CNC Turning
CNC turning is generally faster and more cost-effective than milling for producing round shapes due to the simplicity of its setup and operations, which enable high production rates.
While turning may lead to greater material wastage compared to milling, depending on the design of the part, its speed and ease often make it the preferable choice.
Setup for CNC turning is usually less complex than that for milling, precision is still crucial, and advanced turning machines may include live tooling capabilities that allow for milling operations, adding versatility to the turning process.
Machine Type | Cost per Hour (USD) | Notes |
---|---|---|
3-Axis CNC Machining | $50 – $100 | Simpler machines, suitable for basic parts. |
4-Axis CNC Machining | $75 – $125 | Offers increased flexibility compared to the 3-axis. |
5-Axis CNC Machining | $100 – $150+ | Most complex, ideal for difficult parts. |
Table 3: Estimated CNC Machining Costs per Hour by Machine Type
Processing Time
Processing time is a critical component in CNC machining that significantly impacts the overall production cost. This encompasses all activities from the initial setup to the final handling of the machined parts.
Setup Costs
Setting up a CNC machine is particularly labor-intensive and costly, involving the installation of appropriate tools and fixtures, material preparation, and setting machine parameters, especially for complex designs. Additionally, the programming phase is pivotal, as CNC machines require precise instructions to operate.
The time taken to create and input these programs is influenced primarily by the complexity of the part.
Handling Costs
Handling costs also contribute significantly to the overall expense. Each batch of parts must be carefully loaded into and unloaded from the machine, requiring meticulous handling to avoid damage to both the parts and the machine.
Post-machining handling, which includes cleaning, inspection, and possibly secondary operations like painting or assembly, is necessary to ensure that the parts meet all specifications and are ready for use or delivery. These steps add further labor and time costs to the machining process.
Regional Variations in Labor Costs
Regional variations in labor costs can drastically affect the cost-efficiency of CNC machining operations. In high-cost regions, elevated wages increase the costs associated with machine operation, setup, programming, and handling, driving up overall production costs.
In contrast, lower labor costs in other regions can make it more economical to produce parts, despite similar expenses for other operational costs like electricity and materials.
This disparity often prompts businesses to either relocate their manufacturing operations or outsource them to areas with more favorable economic conditions, optimizing cost efficiency while maintaining production quality.
Additional Cost Considerations in CNC Machining
Tooling and Equipment Costs
Tool wear and replacement are inevitable in CNC machining, significantly affecting production time and costs. Frequent tool changes are necessary when working with harder materials or complex operations, which increases both direct costs (tool pricing) and indirect costs (downtime and labor).
Specialized tooling, like custom fixtures or jigs, is often required for parts with unique geometries or high precision demands, representing a significant upfront investment. These costs can be mitigated by investing in higher-quality tools that last longer and by scaling production volumes to amortize costs more effectively.
Surface Finishing Costs
Surface finishes significantly impact the aesthetic and functional quality of CNC machined parts, influencing overall costs. Basic finishes like as-machined surfaces incur minimal costs, while advanced processes like bead blasting, anodizing, powder coating, and electroplating require additional equipment, materials, and skilled labor, leading to higher expenses.
Each finishing process adds to the processing time and requires various levels of labor intensity, with more complex finishes necessitating extensive prep work and specialized skills, thereby increasing the overall project cost.
Secondary Processes Costs
Secondary operations such as threading, chamfering, and deburring are crucial for achieving the desired functionality and finish of CNC machined parts. These processes require additional specialized tooling and are labor-intensive, especially for parts with complex designs or numerous features, which escalates both time and labor costs.
Automation of these processes can offer cost savings and consistency improvements, although the initial investment in automation technology can be substantial and needs to be justified by sufficient production volumes and operational efficiencies.
Shipping and Handling Costs
The logistics of shipping and handling are critical cost components, especially when delivering CNC machined parts to clients or assembly sites. These costs vary based on distance, delivery options, and the need for protective packaging to ensure parts arrive undamaged.
Managing these expenses involves careful consideration of packaging methods, the choice between standard and expedited shipping, and an understanding of regional labor cost variations to optimize overall cost-efficiency in the project's delivery phase.
Secondary Processes Costs
Secondary operations such as threading, chamfering, and deburring are crucial for achieving the desired functionality and finish of CNC machined parts. These processes require additional specialized tooling and are labor-intensive, especially for parts with complex designs or numerous features, which escalates both time and labor costs.
Automation of these processes can offer cost savings and consistency improvements, although the initial investment in automation technology can be substantial and needs to be justified by sufficient production volumes and operational efficiencies.
Shipping and Handling Costs
The logistics of shipping and handling are critical cost components, especially when delivering CNC machined parts to clients or assembly sites. These costs vary based on distance, delivery options, and the need for protective packaging to ensure parts arrive undamaged.
Managing these expenses involves careful consideration of packaging methods, the choice between standard and expedited shipping, and an understanding of regional labor cost variations to optimize overall cost-efficiency in the project's delivery phase.
Fig. 2: Komaspec's Warehouse
How to Reduce CNC Machining Costs
Reducing costs in CNC machining while maintaining quality and functionality is crucial for optimizing production efficiency and profitability.
Here are strategic approaches to achieve cost-effectiveness:
Optimizing Design for Manufacturing
Simplifying Designs
To reduce CNC machining costs, streamline part designs whenever possible. Complexity and customization significantly drive up costs due to the need for special tooling or fixtures, multiple machine setups, and extended production time.
Custom parts often require unique tools and fixtures, which involve additional design, fabrication, and testing expenses. Complex geometries necessitate multiple machine setups, increasing downtime and labor costs, while intricate programming and planning demand more engineering hours to prepare the job.
By designing parts that can be machined in fewer setups or even a single setup, you can significantly reduce labor and runtime costs. This might involve rethinking the design of the part or combining features that can be machined together.
Here are some ways to simplify part design to reduce costs:
- Avoid sharp, 90-degree internal corners, as these require the machine to stop and reposition the part, increasing machining time and expenses. Instead, using rounded internal corners allows the machine to run continuously, lowering production costs. Ideally, design with an inside corner radius that maintains a length-to-diameter (L) ratio of 3:1 or less and keep internal corner radii consistent whenever possible to further optimize efficiency.
- Parts with deep internal pockets require extensive material removal, additional time, and special tools. Aim to limit pocket depths to four times their length, ideally two to three times the tool's diameter, to stay within the cutting limits of CNC tools. As a best practice, design parts with a length-to-depth ratio of up to 4:1, as deeper pockets become exponentially more expensive to produce.
- Optimize the length of threads by avoiding unnecessarily long threads, as increasing thread length beyond three times the hole's diameter typically does not strengthen the connection but does require special tools and adds time, increasing costs expenses.
- Use standard drill sizes for holes, as non-standard sizes often require end mill tools, increasing expenses. The depth of holes also affects cost; while holes up to ten times the diameter can be machined, they are more challenging and costly. For holes with diameters up to 10 millimeters, design in 0.1-millimeter increments; for diameters above 10 millimeters, use 0.5-millimeter increments. Try to keep the hole length to no more than four times its diameter to optimize cost.
- Parts with small features with a high width-to-height aspect ratio are difficult to machine accurately and increase expenses. Keep all features with a width-to-height ratio below four, and improve their stiffness by connecting them to thicker walls or reinforcing them with bracing support ribs on all four sides.
- Re-consider designing parts with thin walls, as they are fragile, prone to distortion, and difficult to maintain tolerances, leading to increased expenses. Thicker walls provide greater stability and are more cost-effective to machine. If weight is not a critical factor, design metal parts with walls thicker than 0.8 millimeters and plastic parts with walls thicker than 1.5 millimeters.
Fig. 3: Real Time DFM Analysis on the Komacut Platform
Managing Tolerances
Limit the use of tight tolerances to only the essential features of a part, as they increase machining time and require manual inspection. Tight tolerances dictate the level of accuracy needed, which determines the intricacy of the tools used and thus the cost.
By specifying precise tolerances only where necessary and allowing less critical features to follow standard tolerances, you can avoid unnecessary expenses and optimize the machining process. For example:
- ±0.1mm to ±0.05mm: Moving to slightly looser tolerances decreases the need for high-precision tools and reduces machining time.
- ±0.05mm to ±0.02mm: This adjustment involves a substantial increase in complexity and should only be used if critical to the part’s function.
Cost Implications of Tolerances
Utilizing lower tolerances can often be achieved with less sophisticated machinery and less time, resulting in lower costs and fewer rejects.
Although higher tolerances ensure precision, they necessitate more advanced machinery and longer machining times, which increase costs and the rate of rejects if not managed properly.
Fig. 4: CNC Turned Parts from Komacut
Bulk Ordering
Advantages of Bulk Ordering
Bulk ordering of parts can dramatically reduce the cost per unit due to economies of scale. Setup costs, tooling, and even material purchases can be amortized over a larger number of units, decreasing the overall expense.
Examples of Cost Savings
For instance, ordering 1,000 units instead of 100 can spread the fixed setup costs across more items, significantly reducing the cost contribution of these factors per part.
Manufacturers often offer lower prices per unit as order size increases due to the reduced marginal cost of production for each additional unit.
Material Selection
Choosing Cost-Effective Materials
Select materials that adequately meet the project requirements but do not exceed necessary specifications. For example,
- If a part does not require the corrosion resistance of stainless steel, using carbon steel with zinc plating can achieve similar results at a lower cost.
- When high strength is not necessary, choosing aluminum over titanium provides adequate durability while significantly reducing material expenses.
- For components that do not require the wear resistance of hardened steel, selecting a machinable alloy like 6061 aluminum reduces both material and production costs.
Balancing Material Properties with Cost
- Machinability: Softer materials like aluminum are not only cheaper but also easier to machine than harder materials like stainless steel, which requires more robust and expensive tools.
- Shipping Costs: Lighter materials can also reduce shipping costs, which is a considerable advantage for large or bulk orders.
Reducing processing and handling costs.
- To reduce processing and handling costs choose materials that are easy to machine, like aluminum or mild steel, as they require less cutting force, reduce tool wear, and speed up production.
- Select lightweight materials, such as plastics or aluminum, to ease handling, especially for larger parts. Avoid using hard-to-machine materials like titanium or hardened steel unless necessary, as they require specialized tools and longer machining times.
- Selecting readily available materials in standard sizes and consistent quality also minimizes the need for custom preparation and additional adjustments, further cutting costs.
Conclusion
Managing costs in CNC machining requires a deep understanding of several key factors that directly influence the overall expenses of production. Here are the key strategies for cost reduction:
- Optimize the design for manufacturing by simplifying part geometries to reduce the number of machine setups.
- Maintain practical tolerances, applying tight tolerances only where absolutely necessary to minimize machining time and inspection costs.
- Choose materials that are easy to machine and handle, balancing performance requirements with cost-effectiveness.
- Standardize tools, fixtures, and processes to decrease custom setups and streamline production.
- Leverage automation and efficient material flow strategies to reduce manual handling and increase operational efficiency.
- Batch similar parts together to minimize setup changes and maximize machine utilization.
- Minimize the need for secondary operations, such as deburring or additional finishing, to save on labor and handling costs.
FAQs
1. How can I reduce the cost of CNC machining?
The number one impact is to increase batch size; where practical, ordering in larger quantities is going to do the most to reduce part pricing.
Next, simplify designs to minimize complex features and reduce the number of setups. More setups mean either using a higher axis machine or more labor and machine setup costs. Complex features, such as a slope on a part, mean more machining time and multiple tool changes.
Finally, use the loosest possible tolerances that will work for your part design. If you’re not sure, you can discuss your project with your machining supplier and ask for their feedback. Getting these three things right will be 80%+ of the job on cost optimization.
Selecting readily available materials in standard sizes and consistent quality also minimizes the need for custom preparation and additional adjustments, further cutting costs. If you order a non-standard thickness or alloy, cost or minimum order quantities are greatly affected.
2. Why is material selection important in CNC machining?
Choosing the right material affects both the machining process and the cost. Softer materials like aluminum are easier and cheaper to machine compared to harder materials like stainless steel, which require more time and wear down tools faster.
3. How does bulk ordering help reduce CNC machining costs?
Bulk ordering spreads the fixed costs such as setup and tooling across more parts, reducing the cost per unit, and has the biggest impact on part pricing of any factor. It also often secures material discounts and reduces handling and shipping costs per part.
4. What are the practical tolerances in CNC machining?
This depends on the feature and the number of fixturing changes required. A typical rule of thumb for tolerance is ±0.1mm for standard and ±0.05mm for high precision machining, but this depends on part size, feature type, etc.
Linear Dimension Range (mm) | f (fine) | m (medium) | c (coarse) | v (very coarse) |
---|---|---|---|---|
0.5 up to 3 | ±0.05 | ±0.1 | ±0.2 | - |
over 3 up to 6 | ±0.05 | ±0.1 | ±0.3 | ±0.5 |
over 6 up to 30 | ±0.1 | ±0.2 | ±0.5 | ±1.0 |
over 30 up to 120 | ±0.15 | ±0.3 | ±0.8 | ±1.5 |
over 120 up to 400 | ±0.2 | ±0.5 | ±1.2 | ±2.5 |
over 400 up to 1000 | ±0.3 | ±0.8 | ±2.0 | ±4.0 |
over 1000 up to 2000 | ±0.5 | ±1.2 | ±3.0 | ±6.0 |
over 2000 up to 4000 | - | ±2.0 | ±4.0 | ±8.0 |
5. Can the design of a part affect its CNC machining cost?
Yes, the design impacts machining costs significantly. Complex designs requiring multiple setups, high precision, and special tooling will increase costs. Simplifying the design to reduce these needs can lower costs. As a general rule, the more material removed, and the higher the number of different features (threading, chamfering, radii), the higher the machining time and tooling / fixturing changes, and the higher the price.
6. How do I choose the best finish for my CNC machined part?
Select a finish based on the part’s application requirements. Basic as-machined finishes are cheaper, while processes like anodizing or powder coating provide additional properties but at a higher cost. Check out this article.
7. Is it cheaper to machine aluminum or stainless steel?
Aluminum is generally cheaper to machine than stainless steel due to its softer nature, which allows for quicker machining times and less tool wear.
8. What should I consider when setting tolerances for CNC machined parts?
Consider the functional requirements of the part. Set tolerances that ensure operational integrity without being overly tight, as stricter tolerances lead to higher machining costs. Part requirements have a lot to do with how the part is used – is it moving, at high speeds or low speeds? What parts does it need to fit with? etc.
9. How can I ensure high-quality CNC machined parts while keeping costs low?
The most important aspect is to focus on reducing the amount of machine time needed by minimizing machine time and picking a size near that of the raw bar stock, avoiding overly high tolerance or surface finish requirements, and looking at optimal batch sizes for your needs.