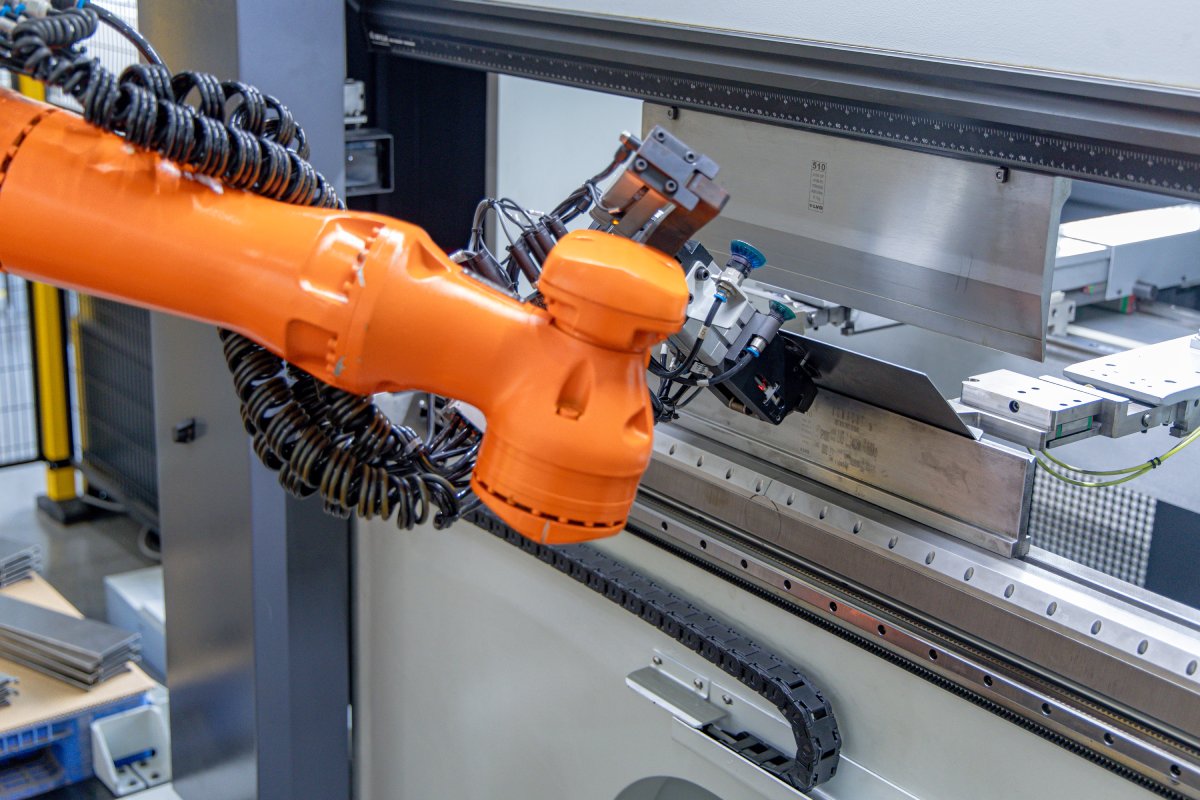
Introduction
Sheet metal bending is vital in modern manufacturing, transforming flat metal sheets into complex shapes. Achieving precise bends ensures product functionality, enhances efficiency, and reduces waste in production.
This article explores the ins and outs of sheet metal bending, from setup and execution to quality control and finishing. Whether you're a seasoned professional or just starting, understanding these key steps will help elevate your manufacturing processes and deliver high-quality results every time.
Key Takeaways
- You will learn how sheet metal is bent into precise forms, with little or no custom tooling, for prototype to mass production quantities.
- Why does precision in bending drive manufacturing efficiency, product quality, and customer satisfaction?
- Understand common bending techniques, such as air bending and bottom bending, and be able to address specific material and design requirements.
2. Common Bending Processes
Sheet metal bending encompasses a variety of techniques to achieve specific shapes and angles, each tailored to the material, design requirements, and production volume. These methods can be broadly classified into manual and automated bending processes.
3. Setting Up to Bend Sheet Metal
The process of setting up for sheet metal bending involves several critical steps to ensure the final product meets design specifications without defects or structural failures.
Part Design Review
Material Check
The material's properties significantly impact its ability to be bent. Not all materials are suitable for sharp radii. For instance, aluminum alloys tend to crack under sharp bending due to their stiffness and lower ductility. Materials with higher ductility, such as mild steel or annealed metals, are better suited for tight bends.
Design Check
Key considerations include ensuring the design adheres to sheet metal bending guidelines. Here are some important ones:
- Minimum Bend Radius: Ensure the bend radius adheres to material-specific guidelines. Too sharp bends can result in cracking, especially in brittle materials like certain aluminum alloys.
- Material Grain Direction: Always design bends perpendicular to the material's grain direction to minimize the risk of cracking, particularly in stiff or brittle materials.
- Relief Cuts: Include relief cuts around bends to prevent mushrooming, wrinkling, or cracking. This helps distribute stress evenly along the bend line.
- Proximity to Edges or Holes: Maintain proper spacing between the bend line and edges or holes to prevent deformation and weakening of the structure.
- Bend Allowance and Deduction: Account for the material's elongation and compression during bending to ensure accurate final dimensions.
- Flat Sections Between Bends: Leave sufficient flat areas between consecutive bends to avoid distortion and ensure proper tool access.
- Tool Clearance: Design with enough clearance for the bending tools, especially for parts with complex geometries or tight spaces.
- Tolerance Considerations: Specify realistic tolerances that accommodate variations in material thickness, machine settings, and springback to avoid rework or rejection.
Bending Process Analysis
Modern manufacturing relies on simulation software to evaluate the feasibility of a design. Bend analysis simulations identify potential collisions between the sheet and tools, verify adequate clearances, and predict material behavior during deformation. These simulations allow engineers to optimize designs for manufacturability, reducing trial-and-error iterations and improving efficiency.
Creating CAM Programs
Once the design is finalized, Computer-Aided Manufacturing (CAM) programs are generated to control CNC bending machines. CAM software converts the design into machine-readable instructions, specifying parameters like bend angle, punch and die selection, and sequence of operations.
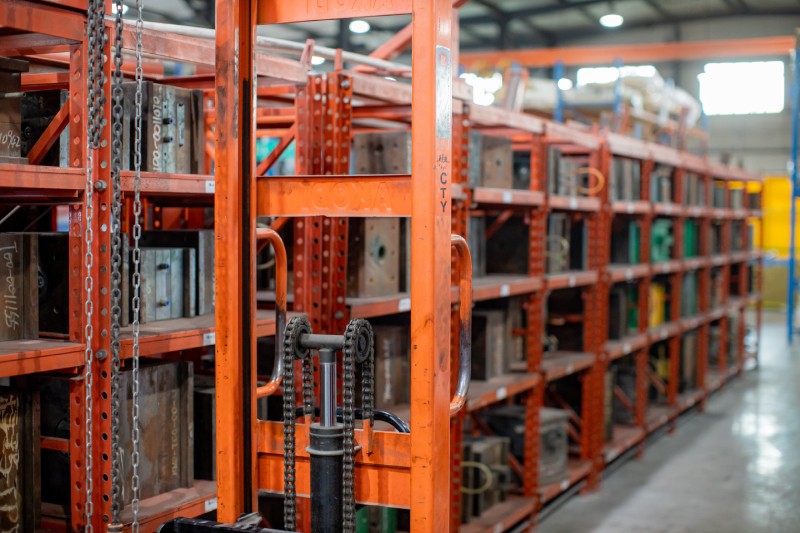
Tool Setup
The selection and configuration of tools play a pivotal role in the bending process.
- Common Tools: Standard punches and dies are used for most applications, with variations in die width and punch radius depending on the required bend angle and material thickness.
- Custom Tooling: For complex geometries or non-standard designs, custom tools may be necessary. This involves fabricating specialized punches, dies, or fixtures to achieve precise bends while maintaining part integrity.
- Forming Tooling: certain specialized forming tools can also be used by CNC bending machines; these include dies for forming sheet metal louvers (venting), creating curved radii on parts, and even creating ribbing for part reinforcement.
Machine Setup
The final step in the setup involves configuring the bending machine based on the material and design requirements.
- Machine parameters, such as bending force, punch speed, and die positioning, are calibrated according to the material's thickness and properties.
- The CAM program is loaded into the machine's control unit, ensuring that the bending sequence is executed accurately.
- Additional factors, such as sheet alignment, clamping pressure, and tool positioning, are carefully adjusted to prevent errors during the operation.
Bending Execution
Once the part is aligned, the actual bending process begins, requiring different techniques depending on the design specifications and material properties. The force required for bending, known as tonnage, varies based on the thickness and type of material.
Post-Bending Steps
After the bending operation, the pressure applied by the punch is gradually released, and the part is removed from the press.
Sequence of Additional Bends
If the part requires multiple bends, each must be performed in the correct sequence to avoid interference with previous bends.
5. Quality Control in Bending
Ensuring precision and consistency during sheet metal bending is critical to achieving high-quality results. Quality control measures are implemented at various stages, from the inspection of the first piece to maintaining standards during mass production.
First Piece Inspection
The first piece inspection is a vital step in the bending process to validate machine settings and ensure the output matches design specifications.
Check for Accuracy and Spring Back
The dimensions, angles, and bend radii are checked against the design requirements using tools like calipers, protractors, or specialized angle-measuring devices. Springback, the material’s tendency to revert slightly toward its original shape after bending, is assessed.
Adjustments and Recalibration
If deviations are detected, the bending machine is recalibrated. Adjustments may include modifying the punch stroke, changing the die or punch to suit the material better, or over-bending slightly to compensate for spring back.
6. Mass Production
Once the first piece inspection is complete, and the setup is validated, the process transitions to mass production.
During this phase, the machine operates at its optimal capacity to produce large quantities of bent parts. Operators monitor the process to ensure the parts remain within tolerance limits. Any issues, such as tool wear, material inconsistencies, or alignment shifts, are addressed immediately to avoid defects in the batch.
Before proceeding with finishing or packaging, each part undergoes a thorough inspection to ensure compliance with quality standards. Key parameters such as bend angles, dimensions, surface condition, and overall structural integrity are checked. Any defects, such as burrs, scratches, or misalignments, are addressed at this stage to avoid compromising the final product's quality.
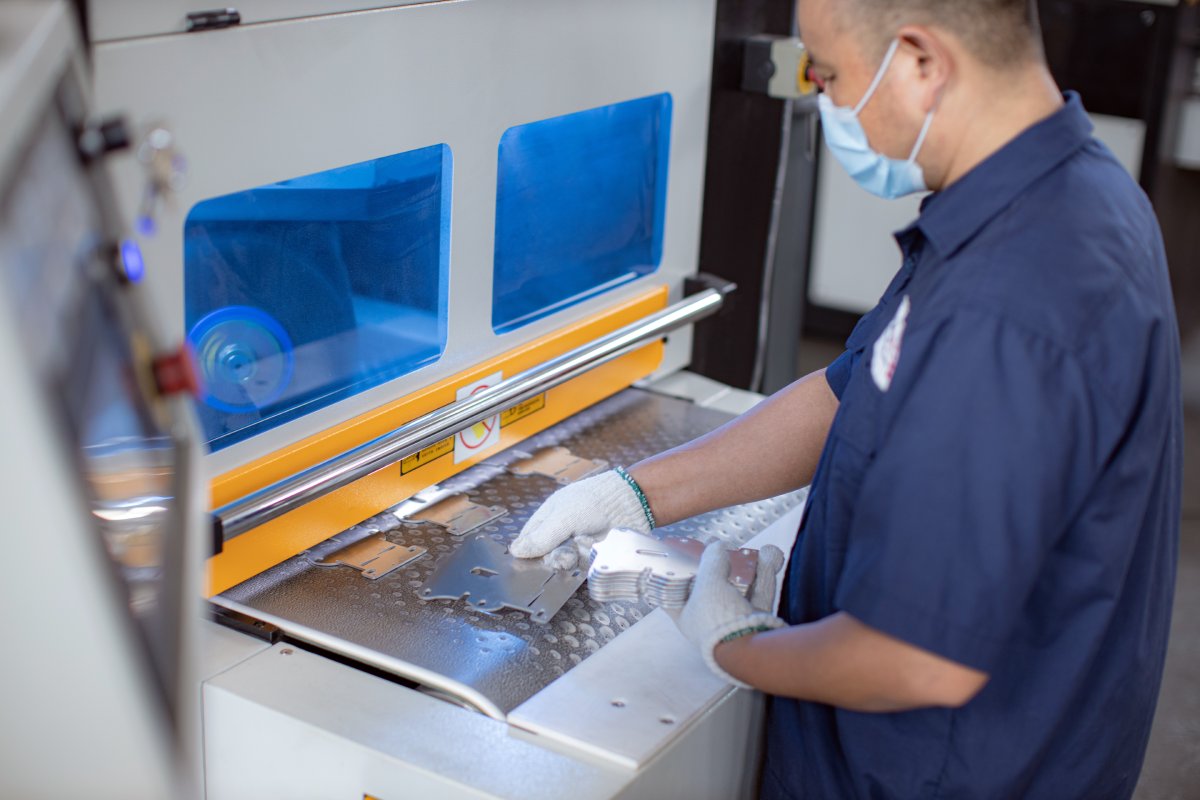
7. Finishing Treatments
Depending on the application and material, various finishing treatments may be applied to enhance the appearance, durability, or functionality of the parts. Depending on the requirements, this can happen before or after the bending process.
- Deburring and Edge Treatment: Sharp edges or burrs caused by cutting or bending are smoothed using grinding, sanding, or tumbling processes to ensure a polished finish.
- Surface Coating: Finishes such as painting, powder coating, or anodizing are applied for corrosion resistance, aesthetic appeal, or added durability. For parts exposed to harsh environments, protective coatings like galvanizing or plating may be used.
- Polishing or Brushing: For parts requiring a clean or decorative appearance, especially in stainless steel or aluminum, brushing or polishing is performed to create a uniform surface texture.
- Assembly or Marking: Some components may undergo partial assembly or be marked with identification tags, serial numbers, or logos to facilitate tracking and branding.
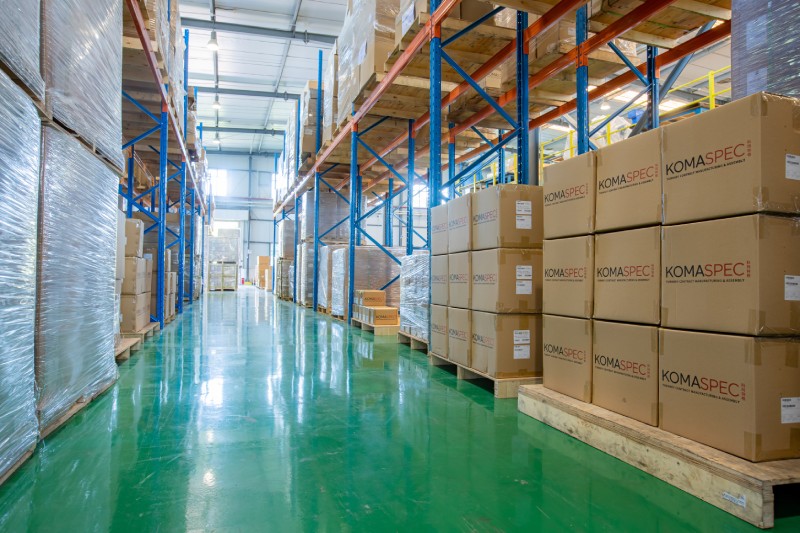
8. Packaging
Proper packaging is essential to protect the finished parts during transportation and storage. The packaging process is tailored to the product's size, weight, and fragility.
- Protective Wrapping: Delicate parts are wrapped in protective materials such as foam, bubble wrap, or plastic to prevent scratches, dents, or other damage. For items with sensitive finishes, non-abrasive materials are used to maintain their appearance.
- Custom Packaging: For irregularly shaped or heavy parts, custom packaging solutions like form-fitting molds, padded crates, or reinforced boxes are used to provide stability during transit.
- Labeling and Documentation: Each package is labeled with relevant details such as part numbers, batch information, and handling instructions. Shipping documentation, including packing lists and inspection certificates, is also included to ensure traceability and smooth delivery.
- Bulk Packaging: For mass production, parts may be stacked with interleaving layers of protective sheets, secured with straps, and palletized for easier handling and shipping efficiency.
Conclusion
Sheet metal bending is an important step in modern manufacturing, requiring precision, expertise, and careful attention to every detail. From design and material selection to machine setup, bending execution, and final packaging, each phase contributes to the overall quality and performance of the finished product.
Accurate bending not only ensures structural integrity and aesthetic appeal but also reduces waste, minimizes rework, and enhances manufacturing efficiency. Whether producing prototypes or engaging in mass production, the ability to maintain high standards of precision directly impacts the reliability and success of the final product.
We encourage you to explore detailed resources available through Komacut or Komaspec. These platforms provide valuable insights, advanced solutions, and expert guidance tailored to your manufacturing needs. Take the next step toward mastering the art of sheet metal fabrication and achieving excellence in your projects.