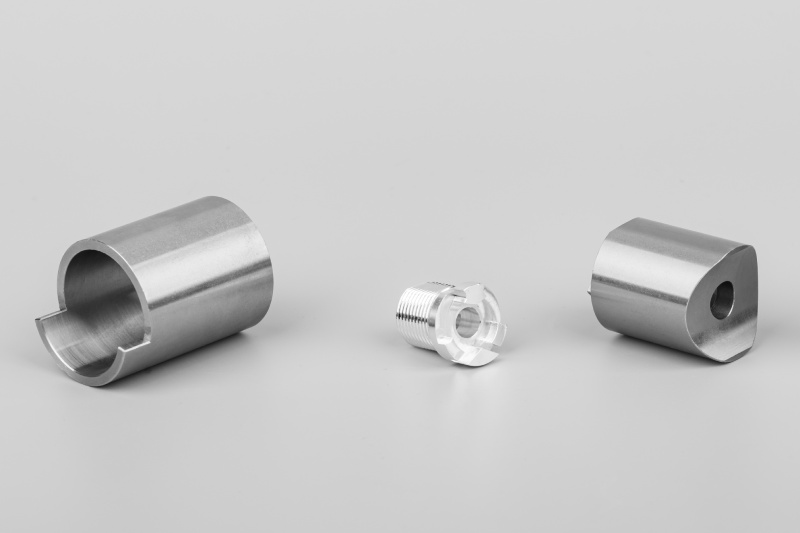
- Introduction
- Plastic Materials for CNC Machining
- Nylon
- PTFE (Polytetrafluoroethylene) or Teflon
- Acetal (POM)
- PEEK
- Polyvinyl Chloride (PVC)
- Polyethylene terephthalate (PET)
- ABS (Acrylonitrile Butadiene Styrene)
- Material Properties and Applications
- How to Select a Plastic Material for CNC Machining
- Factors for Selecting a Plastic Material for CNC Machining
- Application Needs
- Part Needs
- Conclusion
- The Komacut Advantage
- FAQs
Selecting the right plastic material for CNC machining to manufacture parts is a critical decision that can impact both the cost and performance of a project. By following the guidelines outlined in this article you can avoid common pitfalls and make informed decisions so that you can select the right plastic material for your CNC machined parts.
Introduction
One of the primary challenges in plastic material selection for CNC machining is that not all plastic materials are suitable for a particular part Or application. It’s important to select the right material for any part, but selecting a plastic for machining is particularly tricky.
Some plastics also exhibit significant dimensional instability, impacting tolerances, and some also have limited color options. There are strength considerations, resistance to stress cracking, or heat expansion. Application-specific considerations such as chemical resistance, food safety, or self-lubrication can also be an aspect.
The potential cost implications and performance issues associated with incorrect material choices cannot be overstated. Using the wrong material can lead to increased scrap rates, longer lead times, and higher overall production costs. It can also result in parts that do not meet the required specifications, leading to quality issues and customer dissatisfaction.
Fig. 1: CNC Machined Plastic Parts
Plastic Materials for CNC Machining
Several types of plastics can be used in combination with CNC milling and turning, but the choices are generally more limited compared to injection or other fabrication processes, due to the heat and stress introduced to plastic material during the machining process. This means that many standard plastic materials are not widely, or ever, used to manufacture plastic parts by machining.
Nylon
Nylon’s versatility and performance characteristics make it a preferred choice for parts used in various industries manufactured using CNC machining. Nylon is strong, has good impact resistance, and is widely available in block or bar form.
Applications
- Lightweight components like gears, bushings, gaskets, and bearing surfaces, replacing metal parts for weight reduction and fuel efficiency.
- Electrical connectors and insulating parts
- Machine parts like pulleys and rollers
Properties
- Excellent mechanical properties.
- Impact strength.
- Chemical resistance.
- Abrasion resistance.
- Low coefficient of friction.
- Susceptible to water and moisture absorption.
Other Advantages
- Ease of machining.
- Low cost.
PTFE (Polytetrafluoroethylene) or Teflon
PTFE, commonly known by the brand name Teflon, is an engineering thermoplastic. It is suitable for a variety of industrial and consumer applications.
Applications
- Seals and gaskets to make them resistant to chemicals and high temperatures.
- Electrical insulators and components for electronic applications.
- Bearings and Bushings because of their low coefficient of friction and good wear resistance.
- Valve Seats for fluid control applications, benefiting from its chemical inertness and ability to maintain integrity at high temperatures.
- Washers for applications requiring superior chemical resistance and stability.
Properties
- Excellent mechanical properties.
- Low deformation under load.
- High tensile strength.
- Good impact resistance.
- Excellent electrical insulator even at high temperatures.
- Resistant to a wide range of chemicals, acids, and solvents.
- Low coefficient of friction.
Other Advantages
- PTFE itself is often machined in CNC machining operations to create components that require good thermal stability. It can withstand temperatures above 200 degrees Celsius without losing its mechanical properties, making it suitable for high-temperature applications where other plastics would degrade.
- It has the lowest coefficient of friction of any known solid material, providing excellent lubricity and making it ideal for applications such as bearings and seals.
Acetal (POM)
Acetal, or polyoxymethylene (POM), known by the commercial trade name Delrin, is a strong, rigid plastic often used in CNC machining.
Applications
- Ideal for bearings and bushings due to its low coefficient of friction and high dimensional stability.
- Electrical components that require high dielectric strength and resistance to moisture.
- Precision parts due to dimensional stability and ease of machining.
- Automobile parts such as fuel system components, belt buckles, and various mechanical parts.
- Screws, nuts, and other fastening components for its strength and ease of threading.
- Various medical device components due to its biocompatibility and ease of sterilization.
- Valves and valve seats for applications that require precise control and resistance to wear and chemicals.
Properties
- Excellent dimensional stability.
- Exceptional machinability.
- Low friction.
- Low moisture absorption.
Other Advantages
- POM is easy to cut, drill, and shape using CNC machining processes. It is often the best choice for CNC machining plastic parts that require high precision, stiffness, low friction, dimensional stability at elevated temperatures, and low water absorption.
- POM is often used for machining gears because of its high strength, low friction, and excellent wear resistance.
PEEK
PEEK (polyetheretherketone) is a high-performance engineering thermoplastic with very good mechanical properties, including high-temperature resistance, strength, and chemical resistance. PEEK is commonly used in CNC machining for applications where durability and reliability are critical.
Applications
- Seals, bushings, and brackets for high strength-to-weight ratio, thermal stability, and resistance to radiation.
- As PEEK is biocompatible and sterilizable it is an ideal material for medical components and applications
- Bearings, piston parts, and transmission elements because of high temperature and chemical resistance.
- Excellent electrical insulating properties make it suitable for high-performance electrical connectors and insulators.
- Valve seats, and compressor components due to resistance to harsh chemicals and high pressures.
- Semiconductor fabrication equipment because of their low outgassing and high purity.
- Pump parts, valve components, and other equipment in aggressive chemical environments.
- Parts that require compliance with food safety standards, having resistance to high temperatures and chemicals.
- Its excellent wear resistance and low friction make PEEK suitable for machining into bearings, bushings, and other wear-resistant parts.
Properties
- Maintains its mechanical properties at temperatures up to 260°C.
- Highly resistant to a wide range of chemicals, including acids, bases, and organic solvents.
- High tensile strength and stiffness.
- Low coefficient of friction and excellent wear resistance.
- Maintains its dimensions and shape under varying thermal and mechanical conditions.
- Biocompatible and suitable for medical implants and devices.
- Can withstand high levels of radiation without significant degradation.
- Excellent insulating properties.
- Low outgassing.
- Relatively high cost (the most expensive of standard machined materials)
Other Advantages
- PEEK is available in medical grades, making it suitable for biomedical applications such as implants, surgical instruments, and medical devices where biocompatibility and sterilizability are crucial.
- It is inherently flame resistant and generates very low smoke and toxic emissions when exposed to fire
Polyvinyl chloride (PVC)
Polyvinyl chloride (PVC) is a versatile thermoplastic known for its durability and chemical resistance, making it suitable for a wide range of applications including construction, healthcare, automotive, and packaging.
Applications
- Often used for fitting, valves, and couplings due to durability, chemical resistance, and ease of joining.
- Can be used for insulating spacers, bushings, or other parts in electrical assemblies due to its excellent electrical insulating properties.
- Automotive components like bushings, washers, and protective covers because of mechanical strength and resistance to oils and chemicals.
- Components such as pump housings, seals, and custom fittings are made from PVC to ensure their resistance to corrosive chemicals.
- Weather-resistant sign boards and display frames.
- Fittings and housings for marine environments due to PVC’s resistance to saltwater and UV exposure.
- HVAC system parts, such as ducting components and vent covers, are due to PVC’s lightweight and fire-resistant properties.
Properties
- Resistant to many acids, bases, salts, and organic solvents.
- Good tensile strength and impact resistance.
- Excellent electrical insulator.
- Withstands exposure to the elements, including UV radiation, without significant degradation.
- Absorbs very little water.
Other Advantages
- It is available in rigid and flexible forms, offering versatility in use, making it a popular choice for CNC machining applications.
- Parts made of PVC are durable and have a long service life.
- Unlike many other plastics, PVC is inherently flame-retardant. It is self-extinguishing, which means it stops burning when the ignition source is removed. This property is highly valued in the construction, electrical insulation, and transportation industries.
- PVC is relatively inexpensive compared to other engineering plastics like PEEK or PTFE. Its cost-effectiveness makes it a popular choice for large-scale applications, particularly in the construction and infrastructure sectors.
Polyethylene Terephthalate (PET)
Polyethylene terephthalate (PET) is a widely used thermoplastic with excellent properties, making it suitable for various CNC machining applications.
Applications
- Components for packaging machinery, such as guides, rollers, and conveyor parts.
- Food processing equipment, including gears, bearings, and seals, because of its food-grade properties and resistance to chemicals.
- Precision automotive components like gears, bushings, and fasteners.
- Suitable for electrical insulators, connectors, and housings for electronic components.
- Various medical device components such as housings, covers, and supports, take advantage of its biocompatibility and ease of sterilization.
- Gears, cams, and tensioners for textile machinery for their strength, durability, and low friction characteristics.
- Laboratory equipment parts, including containers, holders, and fixtures.
- Printing machine components such as rollers, guides, and feed mechanisms, benefit from its dimensional stability and wear resistance.
Properties
- Excellent tensile strength and rigidity.
- Resistant to a wide range of chemicals, including acids, bases, and solvents,
- Maintains its shape and size under various conditions, offering high dimensional stability, which is crucial for precision parts.
- Low water absorption, ensuring that its mechanical properties remain stable in humid or wet environments.
- Can withstand moderate temperatures without significant deformation or degradation, making it suitable for applications involving heat exposure.
- Excellent electrical insulating properties.
- Good wear resistance, which contributes to its durability and longevity in high-friction applications.
Other Advantages:
- Can be easily machined, molded, and thermoformed, facilitating its use in a variety of manufacturing processes.
- PET is highly recyclable, contributing to environmental sustainability and making it a preferred material in industries that prioritize eco-friendly practices. Recycled rPET can be used to produce new products, reducing the environmental impact of plastic waste.
ABS (Acrylonitrile Butadiene Styrene)
ABS is a widely used thermoplastic known for its excellent mechanical properties, impact strength, heat resistance, machinability, and relatively low cost making it a popular choice for CNC machining applications.
Applications
- Automobile dashboard parts, instrument panels, and trims.
- Various medical device housings and components that do not require sterilization.
- Housings and structural components of home appliances.
- Components for blenders, mixers, and coffee makers.
- Various small parts and enclosures for machinery and equipment.
Properties
- It is a relatively tough but lightweight and low-cost material, able to withstand heavy impacts without shattering.
- Has a relatively low density, making it lightweight.
- Has good dimensional stability.
- Resistant to a wide range of chemicals, including acids and alkalis.
- Moderate heat resistance, with a melting point typically between 200°C to 240°C.
- Some ABS grades are flame retardant, making them suitable for applications where fire safety is a concern.
- Good electrical insulating properties.
- Easy to machine, drill, and cut, allowing for the creation of intricate shapes and designs.
Other advantages
- ABS parts are often used as prototypes before mass production.
- One of the key advantages of ABS is its high impact strength, which allows it to withstand sudden loads and impacts without breaking or cracking. This property makes it ideal for parts that may be subjected to rough handling or impacts
- It can be easily finished and painted, providing a smooth and aesthetically pleasing surface in many colors and textures.
- It is recyclable, allowing it to be reused, contributing to sustainability.
Material Properties and Applications
Material | Strength | Hardness | Machinability | Cost | Typical Applications |
---|---|---|---|---|---|
Nylon | High | Medium | Medium | Medium | Gears, Bushings, Bearings, Wear parts |
POM | High | High | Excellent | Medium | Gears, Bushings, Bearings, Auto parts |
PEEK | High | High | Difficult | High | Aerospace, Auto, Medical, Oil & Gas |
PVC | Medium | Medium | Easy | Low | Construction, Healthcare, Packaging |
PET | Medium | Medium | Easy | Low | Packaging, Textiles, Engineering parts |
PTFE | High | Low | Difficult | High | Seals, Gaskets, Bearings, Electrical parts |
ABS | Medium | Medium | Easy | Medium | Prototyping, Auto, Consumer goods |
Table 1: Comparison of Material Properties and Their Applications
How to Select a Plastic Material for CNC Machining
Selecting the right plastic material for CNC machining is indeed a critical decision, as it significantly influences the performance, cost, and quality of the final product. Several factors need to be considered when choosing a material:
Consider the part type
- Is it a bushing, an enclosure, a shaft, a gear?
- What are the characteristics of this type of part? Does it need to be smooth and frictionless, or is strength the priority
Consider Part Use
Determine the specific requirements of the part, including mechanical properties (strength, hardness, etc.), dimensional tolerances, surface finish etc.
Consider the application
- Does your target application have any special requirements for the parts in terms of electrical conductivity, self-lubrication, etc.?
- What kind of environment is the application – is it highly corrosive? Is there a high degree of exposure to UV or weathering? High heat?
- Are there regulatory or certification requirements?
Finalize Requirements & Selection Criteria
Based on the product and application requirements, establish criteria for selecting the plastic type, considering factors such as machinability, cost, availability, and suitability for the application.
- Shortlist Material Options - Shortlist your potential materials and then evaluate trade-offs between material properties, cost factors, and application requirements.
- Consult References: Refer to material selection guides, handbooks, and databases to compare the properties of different plastics and their suitability for CNC machining.
- Cost Analysis: Compare the cost of each material, including raw material cost, machining costs, and any additional costs (e.g., surface treatment, post-machining operations).
- Final Selection: Based on the above considerations, select the plastic material that best meets the requirements for the CNC machining process.
Fig. 2: Simple CNC Machined Parts Made of Plastic
Factors for Selecting a Plastic Material for CNC Machining
Material Properties
Tensile strength, yield strength, hardness, and ductility are important mechanical properties. Higher tensile strength and hardness are desirable for parts subjected to high loads, while ductility is important for parts that require deformation without breaking.
Thermal Properties
Thermal conductivity and coefficient of thermal expansion are important for parts subjected to temperature variations. High thermal conductivity helps in dissipating heat generated during machining, while a low coefficient of thermal expansion ensures dimensional stability at different temperatures.
Chemical Properties
Corrosion resistance and chemical compatibility are crucial for parts exposed to corrosive environments or chemicals.
Machinability
Factors such as material machinability, complexity of the part, and machining time. Materials that are easy to machine, may result in shorter machining times compared to harder materials.
Costs
Cost-effectiveness in material selection involves evaluating the cost per kilogram of material and the machining time required to produce the part. Some materials may have a higher initial cost but offer cost savings in terms of reduced machining time.
Application Needs
Selecting materials based on the operational environment and final product requirements involves considering the following important factors:
- Corrosive Environments - Certain plastics offer excellent chemical and corrosion resistance and are suitable for applications in corrosive environments, such as moisture with salts, acidic environments, high temperatures, pollutants, and organic chemicals.
- Electrical Conductivity - Plastic materials have low electrical conductivity and are useful as insulators and casing to avoid electrical leakages and shocks.
- Food Grade Applications - Many plastics are food-grade and should be selected for applications in food processing or medical industries. ABS, PET, and PP are common selections for food-grade materials, while fiberglass blended plastics should be avoided.
Part Needs
Consideration of specific part requirements, such as wear resistance, weight, and hardness, is crucial for material selection.
- Wear Resistance - Many plastics offer good wear resistance and are suitable for parts subjected to wear, such as gears and bushings.
- Weight - For applications where weight is a critical factor, certain plastics, which are lightweight, should be selected.
- Hardness - Plastic materials with high hardness are suitable for parts requiring high wear resistance and durability.
Conclusion
Selecting the right plastic material involves a step by step consideration of the application, the part type and geometry, and the final performance required. The good news is that by following our guidelines, and with the right feedback from your machining supplier, highlighting the best options aren’t as difficult as it appears.
The Komacut Advantage
Many companies struggle to find reliable and cost-effective suppliers for low and medium-volume production – prototyping companies charge high set-up costs and per-piece pricing; larger manufacturers are not interested in orders of several hundred or even thousand pieces. Not to mention the time and expertise needed to manage and coordinate with these suppliers. Komacut is a solution to bridge the gap between prototyping and mass production, with instant quotes, easy management, and flawless execution from quote to order to delivery.
For more information on designing and manufacturing CNC machining and machined parts, please visit the Komacut website. Instant quotations and design feedback, a range of materials, engineering design guidelines, and more - visit Komacut today for superior CNC machining solutions.
FAQs
What are the most commonly used plastics in CNC machining?
Commonly used plastics in CNC machining include ABS, polycarbonate, nylon, PEEK, Delrin (acetal), and PTFE (Teflon). Each of these materials offers unique properties suitable for various applications.
How do I determine which plastic is best for my project?
To determine the best plastic for your project, consider factors such as mechanical properties, thermal resistance, chemical compatibility, and cost. Additionally, the specific requirements of your application, such as load-bearing capacity, wear resistance, and environmental conditions, should guide your selection.
What are the advantages of using plastic over metal in CNC machining?
Plastics offer several advantages over metals, including lighter weight, corrosion resistance, lower cost, and ease of machining.
How does the machinability of plastics compare to metals?
Plastics generally have better machinability compared to metals due to their lower hardness and density. They require less cutting force and can be machined at higher speeds, reducing tool wear and production time. However, some plastics may have specific challenges, such as melting or deforming under high temperatures, which need to be managed during machining.
What surface finishes can be achieved with CNC-machined plastics?
CNC-machined plastics can achieve a variety of surface finishes depending on the machining process and tools used. Common finishes include a smooth, polished finish, matte or textured finishes for improved grip or reduced glare, and precision finishes for tight tolerance parts.
Are there any special considerations for machining reinforced plastics?
Reinforced plastics, such as those with fiberglass or carbon fiber, require special considerations due to their abrasive nature. These materials can cause increased tool wear and may require the use of carbide or diamond-coated tools.
How does production volume impact the choice of plastic material for CNC machining?
For low production volumes, CNC machining is a cost-effective method for producing plastic parts and is often used for prototyping or pilot productions due to the lack of any requirement for mold or tooling investment. However, for medium to high-volume production, other manufacturing methods such as vacuum casting or injection molding will have a definite cost advantage.
Can recycled materials be used in CNC machining?
Yes, certain recycled materials, such as recycled PET (rPET), can be used in CNC machining. They can offer cost savings and environmental benefits but should be evaluated for consistency and performance compared to virgin materials. In general, plastics with a high (25%+) percentage of recycled content tend to be more brittle and have degraded physical properties.