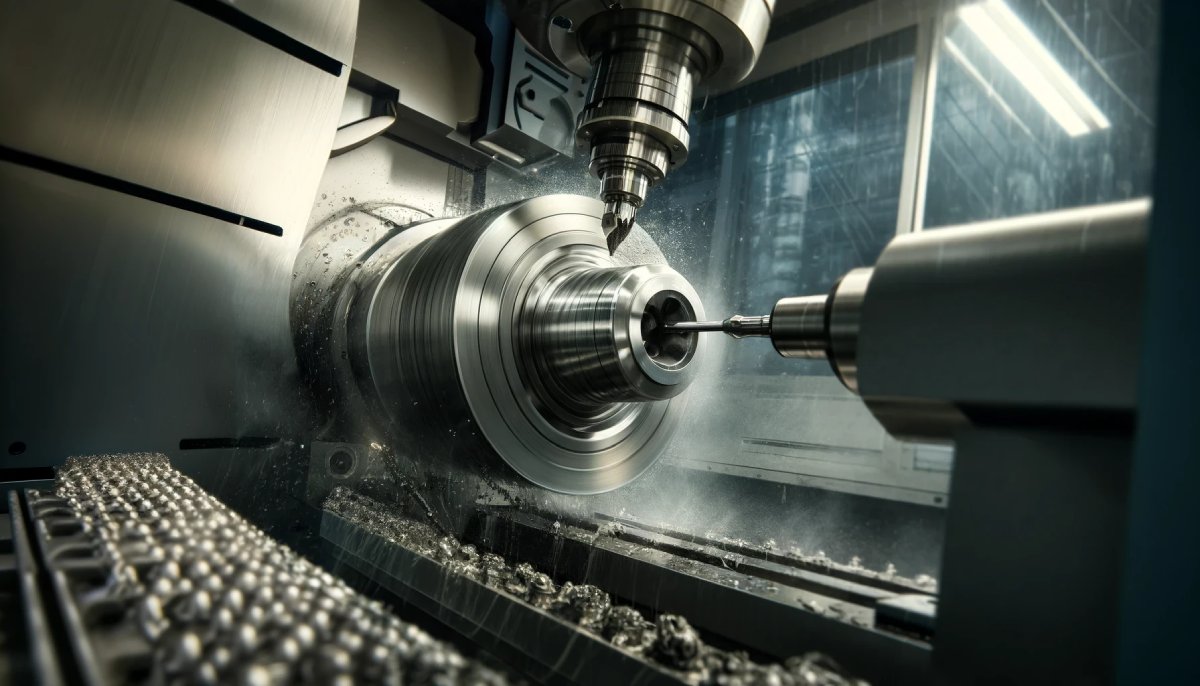
- Introduction
- What is CNC Milling?
- What is CNC Turning?
- CNC Milling vs CNC Turning: Which Process to Choose?
- What Are the Differences Between CNC Milled and CNC Turned Parts?
- Real-World Examples
- Hybrid Machines
- Conclusion
- Komacut
Introduction
CNC milling and CNC turning are both precision manufacturing processes operated by computer numerical control (CNC) cutting machines, which enable high accuracy and repeatability in producing parts. The difficult thing can sometimes be in identifying which type of part is which, and since the process, tolerances, cost and supplier selection are directly linked to the part type, this is a more critical question that it might appear.
There are multi-axis CNC milling machines (from the most common being 3-axis, with 4-axis and 5-axis machining centers for higher complexity) that allow the production of even more complex shapes in a single set-up.
Because of the generally symmetrical nature of the cutting (as the workpiece is moving), this process is generally used to create cylindrical and round parts, though it can also be used to make hexagonal parts as well.
On the other hand, CNC turning involves holding the material in a chuck and rotating it at high speeds while a stationary tool is moved into place to cut away material and shape the part. Because of the generally symmetrical nature of the cutting (as the workpiece is moving), this process is generally limited to creating cylindrical or round shapes.
Fig. 2: CNC Milling vs CNC Turning
What is CNC Milling?
CNC milling operates on a fundamental concept where the excess material is removed from a stationary workpiece using a rotating cutting tool. This process allows for precise cuts and the removal of material in a controlled manner, shaping the workpiece into the desired form. The cutting tool can move along multiple axes, enabling the creation of a variety of shapes, slots, holes, and contours. The ability of the tool to rotate at high speeds and in different directions, combined with the stationary position of the workpiece, ensures high precision and flexibility in the manufacturing process.
CNC milling, with its ability to perform complex cuts and create intricate shapes, is ideally suited for parts with complex geometries, including prototypes, tooling, and components that require precise features on multiple faces. The flexibility of milling machines, especially those with multiple axes, allows for the production of parts with intricate designs in a single setup, reducing the need for multiple operations and thereby increasing efficiency and accuracy.
Types of Milling Machines
The variety and capability of CNC milling machines are categorized based on the number of axes they can operate on, which directly impacts the complexity of the parts they can produce. A 3-axis milling machine moves the cutting tool in three directions, X, Y, and Z, allowing for operations on the plane surfaces of the workpiece. It's suitable for a wide range of parts but has limitations in terms of the complexity of geometries it can efficiently produce.
Advancements in technology have led to the development of 5-axis milling machines, which add two more axes of movement, allowing the cutting tool or workpiece to be rotated, thereby enabling the machining of complex parts from virtually any direction in a single setup. This capability significantly reduces the need for multiple setups, improving precision and reducing the time and cost associated with the production of intricate parts.
The choice between 3-axis, 5-axis, and other types of milling machines depends on the part's complexity, the precision required, and the efficiency needed in the manufacturing process. Utilizing the capabilities of each type of milling machine allows the manufacturer to select the most appropriate and cost-effective method for producing parts, that meet the required specifications and quality standards.
Fig. 3: CNC Milling Machine
What is CNC Turning?
Conversely, CNC turning is most efficient for parts that are cylindrical or circular, producing them with a high level of precision and speed. It is particularly effective for projects requiring symmetrical parts like rods, shafts, and bushings. The turning process is generally faster and less expensive for these types of geometries, offering better surface finishes and quicker turnaround times.
CNC turning operates on a fundamentally different principle from milling, primarily characterized by the rotation of the workpiece as opposed to the tool. In this process, the material to be shaped is secured in a chuck and rotated at high speeds, while a stationary cutting tool is brought into contact with it to remove the material. This setup is especially efficient for manufacturing symmetrical parts along a central axis, such as cylinders, cones, or disks.
The key advantage of CNC turning lies in its simplicity and efficiency in producing round or tubular shapes. The computer-controlled ability allows for precise control over the cutting speed, depth, and feed rate, which contributes to achieving high levels of precision and repeatability in the manufacturing process.
Turning operations encompass a variety of techniques to achieve different features on a workpiece:
Operation | Description |
---|---|
Facing | This operation cuts a flat surface perpendicular to the workpiece's rotating axis, typically at one or both ends of the part. |
Grooving | This involves cutting a narrow groove on the exterior or interior of the part. It's often used for O-ring seats and similar features. |
Threading | A critical operation where the tool is used to carve threads, both internal and external, for screws, bolts, and fittings. The precision of CNC allows for the creation of highly accurate threads tailored to specific standards. |
Parting | Also known as cutting off, this process slices a piece from the rest of the material, essentially separating it after all other machining operations are completed. |
Table 1: Machining Operations
Each of these operations utilizes the turning process's unique capabilities to efficiently shape and detail a workpiece. Turning's rotating workpiece and stationary tool setup make it exceptionally suited for parts that require cylindrical shapes and features, utilizing the natural motion of rotation to achieve the desired geometry with high efficiency and precision.
Fig. 4: Turning Center
CNC Milling vs CNC Turning: Which Process to Choose?
The decision between milling and turning should be based on the part's geometry, the required precision, the material, and the production volume. Choosing the right process can lead to reduced production times, lower costs, and potentially higher-quality parts. A clear understanding of the differences between these processes allows engineers and manufacturers to make informed decisions, optimizing the production process for efficiency, cost, and quality, ultimately ensuring that the final product meets the required specifications and performance standards.
When deciding whether to use CNC milling or CNC turning for a manufacturing project, several critical factors must be considered to ensure the chosen process aligns with the project's requirements. These factors include part shape and features, production quantities, material type, and required accuracy.
Part Shape and Features
The geometry of the part you intend to produce is perhaps the most significant factor.
- CNC milling is the preferred method for parts with complex geometries, including those requiring multiple faces, intricate patterns, or detailed features such as pockets and slots. It also works well for parts with features that need to be cut on multiple faces in a single setup as the cutting tool can move across different axes.
- CNC turning is ideal for parts with cylindrical shapes or features that are symmetrical around an axis, such as shafts, cones, and disks.
Production Quantities
The volume of parts needed can also influence the choice between milling and turning. CNC turning can be more efficient and cost-effective for producing high volumes of parts, particularly if the parts are round or cylindrical. This efficiency comes from the turning process's faster setup times and quicker machining of such shapes.
Meanwhile, for low to medium volumes or when the parts require extensive milling due to their complexity, CNC milling might be more appropriate despite potentially higher costs.
Material
CNC Milling
- Metals – the harder the metal the more difficult to machine, so certain part geometries can be challenging as milling is generally making more complex parts; too high a speed and too hard a material will result in chatter and poor machining tolerancing.
- Plastics – milling can handle a wide variety of materials, and there is generally more control over the transfer of heat and vibration into the part vs turning
CNC Turning
- Metals – turning can effectively machine a wide range of metals, including aluminum, steel, brass, copper, titanium, and various alloys. As turning is handling generally simpler part geometries, it can effectively machine parts. Care must be taken when fixturing low turned parts to prevent deformation.
- Plastics – a wide variety of plastics such as nylon, polycarbonate, acetal (Delrin), and PTFE (Teflon), can be machined using CNC turning. CNC turning can also handle certain composite materials, such as carbon fiber-reinforced plastics and fiberglass, depending on their composition and properties.
Brittle Materials
- CNC turning may not be the best choice for machining brittle materials like ceramics, as the turning process can exert significant cutting forces that may lead to chipping or cracking.
Accuracy & Precision
Both CNC milling and turning offer high precision and tight tolerances, but the nature of the part's required accuracy can tip the scales toward one process. For parts requiring precise tolerances on radial features or smooth surface finishes, CNC turning might be the better option. Conversely, if the part demands high accuracy on complex surfaces or intricate details across multiple faces, CNC milling would likely be more suitable.
Here's a generalized table outlining typical tolerance ranges for turning operations across different materials:
Material | Standard Precision Tolerance Range (inches) | High Precision Tolerance Range (inches) | Standard Precision Tolerance Range (millimeters) | High Precision Tolerance Range (millimeters) |
---|---|---|---|---|
Aluminum | ±0.002 to ±0.005 | ±0.001 to ±0.002 | ±0.051 to ±0.127 | ±0.025 to ±0.051 |
Steel | ±0.002 to ±0.005 | ±0.001 to ±0.002 | ±0.051 to ±0.127 | ±0.025 to ±0.051 |
Stainless Steel | ±0.003 to ±0.006 | ±0.001 to ±0.003 | ±0.076 to ±0.152 | ±0.025 to ±0.076 |
Brass | ±0.002 to ±0.005 | ±0.001 to ±0.002 | ±0.051 to ±0.127 | ±0.025 to ±0.051 |
Copper | ±0.002 to ±0.005 | ±0.001 to ±0.002 | ±0.051 to ±0.127 | ±0.025 to ±0.051 |
Titanium | ±0.004 to ±0.008 | ±0.002 to ±0.004 | ±0.102 to ±0.203 | ±0.051 to ±0.102 |
Plastics | ±0.002 to ±0.005 | ±0.001 to ±0.002 | ±0.051 to ±0.127 | ±0.025 to ±0.051 |
Composites | ±0.003 to ±0.006 | ±0.002 to ±0.003 | ±0.076 to ±0.152 | ±0.051 to ±0.076 |
Ceramics | ±0.004 to ±0.008 | ±0.002 to ±0.004 | ±0.102 to ±0.203 | ±0.051 to ±0.102 |
Table 2: Material Tolerance Ranges
These tolerance ranges are generalized and may vary based on factors such as the specific machining process, machine condition, tooling quality, part complexity, and customer requirements.
Factors | CNC Turning | CNC Milling |
---|---|---|
Part Geometry | Cylindrical and axially symmetrical parts | Complex contours and irregular geometries |
Production Volume | Efficient for high-volume cylindrical parts | More flexible for low to medium volume and prototyping |
Material Properties | Suitable for softer materials like aluminum, brass | Handles harder materials like steel, titanium |
Accuracy Requirements | Good for dimensional accuracy on cylindrical features | Achieves higher dimensional accuracy and tight tolerances |
Surface Finish | Excellent surface finish on cylindrical surfaces | Smooth surfaces on flat and irregular geometries |
Tool Access and Clearance | Limited access to complex features | Better access to deep recesses and intricate details |
Fixture Design and Setup | Simple work-holding setups | May require more complex fixtures for irregular parts |
Cost Considerations | Lower per piece and setup costs | Higher per piece and setup costs |
Lead Time and Turnaround | Quicker setup and turnaround times | Longer setup times, especially for complex parts |
Tool Life and Maintenance | Longer tool life and lower maintenance requirements | Shorter tool life and potentially higher maintenance needs |
Skill and Expertise | Easier to learn and operate for novice operators | Requires advanced programming and setup skills |
Table 3: Comparison of CNC Turning and CNC Milling Processes
What Are the Differences Between CNC Milled and CNC Turned Parts?
Understanding the differences between CNC milled and CNC turned parts can help in choosing the right process for your manufacturing needs. Both processes have unique capabilities and can sometimes be used interchangeably, depending on the part's requirements.
Parts that Can Be Done by Both Processes
Some parts can be produced using either CNC milling or CNC turning. For example, cylindrical parts can be turned to achieve precise diameters and smooth finishes, or they can be milled if additional features, such as slots or flat surfaces, are required. The choice between milling and turning depends on factors such as complexity, volume, and precision requirements.
Feature | CNC Milling | CNC Turning |
---|---|---|
Part Geometry | Complex shapes, contours, and irregular geometries | Cylindrical and axially symmetrical parts |
Material Removal | Stationary workpiece, rotating cutting tool | Rotating workpiece, stationary cutting tool |
Axes of Movement | Multiple axes (3, 4, 5-axis machines) | Typically 2 axes (X and Z) |
Surface Finish | Smooth surfaces on flat and irregular geometries | Excellent finish on cylindrical surfaces |
Production Volume | Flexible for low to medium volumes | Efficient for high-volume cylindrical parts |
Tool Access and Clearance | Better access to deep recesses and intricate details | Limited access to complex features |
Setup and Fixturing | More complex setups, multiple fixtures may be required | Simple work-holding setups |
Typical Parts | Engine components, custom gears, aerospace parts, enclosures | Bushings, rings, shafts, flanges |
Lead Time and Turnaround | Longer setup times for complex parts | Quicker setup and turnaround times |
Tool Life and Maintenance | Shorter tool life, higher maintenance needs | Longer tool life, lower maintenance requirements |
Cost Considerations | Higher per piece and setup costs | Lower per piece and setup costs |
Accuracy and Precision | High accuracy on complex surfaces | Good accuracy on cylindrical features |
Material Suitability | Handles harder materials like steel, titanium | Suitable for softer materials like aluminum, brass |
Table 4: Differences Between CNC Milled and CNC Turned Parts
Real-World Examples of Milled vs Turning Parts
Here are some examples of parts produced by CNC turning, and CNC milling to understand why certain parts are better suited to each process.
CNC Turning Examples
- Bushing - Bushings are typically cylindrical parts used to reduce friction between two surfaces. Turning is ideal for producing bushings because it efficiently shapes these parts from round stock material, ensuring uniformity and precision.
- Ring - Rings, whether used in machinery for sealing, bearings, or decorative purposes, require precise circular dimensions and smooth finishes. CNC turning excels at creating such features due to its ability to rotate the workpiece, allowing for even cutting along the entire circumference.
- Shafts - Shafts are long, cylindrical components often used to transmit power in machinery. CNC turning is ideal for creating shafts because it can efficiently produce the smooth, cylindrical surfaces and precise diameters required for these components to fit and function properly within mechanical systems.
- Flanges - Flanges are used to connect pipes, valves, pumps, and other equipment to form a piping system. They often require a precise circular shape with holes drilled at specific intervals. While the basic shape is cylindrical, making turning suitable, precise hole placement can be achieved through secondary milling operations, demonstrating the versatility of combining processes.
Fig. 5: CNC Turned Parts
CNC Milling Examples
- Complex Engine Components - Engine parts such as pistons or engine blocks feature intricate geometries, including recesses, holes, and specific patterns that cannot be easily achieved through turning. CNC milling can precisely create these complex features by moving the cutting tool across multiple axes.
- Custom Gears - Gears have detailed profiles that require precise cutting to ensure smooth operation. The versatility of CNC milling allows for the creation of custom gear profiles, including the specific teeth shapes and sizes, as well as the necessary bore and keyways, with high precision.
- Aerospace Components - Many aerospace components, such as airframe structures or brackets, have complex shapes and stringent tolerance requirements. CNC milling is capable of producing these components by precisely removing material to achieve the specific contours and features necessary for aerospace applications, where both the shape and the strength-to-weight ratio are critical.
- Enclosures - Enclosures for electronic devices or machinery often require precise cutouts, threading for screws, and complex shapes to house various components snugly. CNC milling can accurately produce these features, accommodating the intricate designs and tight tolerances required for electronic housings.
- Customized Tooling and Fixtures - Tooling components like molds, jigs, and fixtures often have unique geometries tailored to specific manufacturing processes or products. CNC milling provides the flexibility to create these custom geometries, regardless of the complexity, with the precision necessary for the tooling to function correctly. With capabilities to reach tolerances of a standard ±0.1mm up to ±0.02mm for certain designs and with high-quality equipment, CNC milling is unmatched by other mass production processes, except the much slower, more expensive, and more limited wire-cutting process.
- Prototypes of Consumer Products - Many consumer products, from smartphone cases to kitchen gadgets, start as prototypes which will need mass production tooling to produce the precise dimensions and often complex, aesthetic shapes required. For the prototype and pilot stages though, this is often unrealistic as tooling once started is expensive and complex, and changes are common at the early stages of development. CNC milling is capable of producing these prototypes with the detail and accuracy needed to test form, fit, and function before mass production begins.
Fig. 6: Milled Metal Part
Hybrid Machines
As manufacturing technology is evolving, the distinction between CNC milling and CNC turning has become increasingly blurred with the advent of multitasking machines. These advanced machines are designed to combine the capabilities of both turning and milling into a single unit, offering a seamless integration of processes for the manufacture of complex parts. This hybrid approach not only enhances the versatility of CNC machining but also significantly reduces the time and effort required to produce parts with intricate geometries and tight tolerances.
Multitasking machines, often referred to as mill-turn centers or multitasking centers, are equipped with both rotating tools and the ability to rotate the workpiece, enabling them to perform a wide range of operations traditionally associated with both milling and turning. This means that parts requiring both cylindrical and complex milled features can be produced in one setup, reducing the need for multiple setups and operations.
However, the sophistication and versatility of these multitasking machines come at a higher cost compared to traditional, single-process CNC machines. The initial investment in a multitasking machine is typically higher due to its complex design and the advanced control systems required to coordinate the combined milling and turning operations. The programming for these machines can be more complex, potentially requiring higher skill levels from operators and programmers.
CNC milling and CNC turning technology reveal distinct differences, each with its strengths and specialties. CNC milling, with its capability for intricate and complex geometries, excels in creating parts that demand precision across multiple axes and detailed features. It offers unparalleled versatility for producing components with sophisticated designs, from prototypes to custom tooling. On the flip side, CNC turning shines in the realm of symmetrical parts, such as shafts and flanges, where its efficiency in handling cylindrical geometries can be leveraged to achieve high precision and excellent surface finishes cost-effectively. Hybrid machines offer another albeit expensive option for producing complex parts by integrating milling and turning capabilities into a single machine.
The Komacut Advantage
As we recognize the importance of selecting the appropriate machining process to meet specific project needs, we invite manufacturers and engineers to explore platforms like Komacut. Check out the Komacut website to see how you can streamline your manufacturing process, getting access to advanced CNC machining services, including both milling and turning, as well as the expertise to optimize the selection and execution of these processes for your projects.
FAQs
What is the difference between CNC milling and CNC turning?
CNC milling and CNC turning are distinct machining processes, primarily differing in how they shape workpieces. CNC milling involves a stationary workpiece and a rotating cutting tool that removes material to create complex shapes. In contrast, CNC turning revolves around a rotating workpiece while a stationary cutting tool shapes it, primarily suitable for cylindrical or round parts.
What are the advantages of CNC milling over CNC turning?
CNC milling offers several advantages over CNC turning, particularly in its ability to craft intricate shapes and features. With its multi-axis capabilities, CNC milling machines can produce complex geometries efficiently, making them ideal for parts with irregular contours or detailed surfaces. Additionally, milling excels in handling materials that are challenging to turn, such as hardened steels and exotic alloys.
What are the limitations of CNC turning compared to CNC milling?
While CNC turning is highly efficient for producing cylindrical or symmetrical parts, it has inherent limitations when it comes to complex geometries. Turning processes are generally not suited for parts with intricate features or irregular shapes, as the stationary cutting tool is constrained to shaping the rotating workpiece along its axis. CNC turning may face challenges when working with materials that are difficult to cut or prone to chipping, limiting its applicability in certain manufacturing scenarios.
How do I determine whether to use CNC milling or CNC turning for my project?
The decision between CNC milling and CNC turning hinges on various factors, including the part's geometry, production volume, material properties, and required accuracy. For parts with complex shapes or intricate features, CNC milling is typically preferred due to its versatility and capability to handle multifaceted geometries. Conversely, CNC turning is more suitable for cylindrical parts or high-volume production runs, offering efficiency and cost-effectiveness in shaping symmetrical components.
Can CNC milling machines produce parts with cylindrical features?
While CNC milling machines are primarily associated with crafting complex shapes and irregular geometries, they can also produce parts with cylindrical features. However, achieving cylindrical shapes through milling may involve additional setup and tooling considerations compared to turning processes.
What types of materials can be machined using CNC milling and CNC turning?
Both CNC milling and CNC turning processes are versatile and can work with a wide range of materials, including metals, plastics, and composites. Metals commonly machined include aluminum, steel, brass, copper, titanium, and various alloys. Plastics like nylon, polycarbonate, acetal (Delrin), and PTFE (Teflon) are also suitable for machining. Certain composite materials, such as carbon fiber-reinforced plastics and fiberglass, can be processed using CNC milling and turning techniques, depending on their composition and properties.
What are the typical tolerances achievable with CNC milling and CNC turning?
CNC milling and CNC turning processes offer high precision and tight tolerances, ensuring parts meet stringent dimensional requirements. The achievable tolerances depend on various factors, including the specific machining process, machine condition, tooling quality, part complexity, and customer specifications. In general, typical tolerance ranges for CNC machining operations range from ±0.001 to ±0.008 inches (±0.025 to ±0.203 millimeters), varying based on material type, machining parameters, and part design considerations.
Can CNC milling and CNC turning be combined in a single machining process?
Yes, advancements in machining technology have led to the development of multitasking machines capable of integrating both milling and turning operations into a single setup. These multitasking machines, also known as mill-turn centers or multitasking centers, offer seamless coordination between rotating tools and workpiece rotation, enabling a comprehensive approach to part manufacturing. By combining milling and turning capabilities, these machines enhance efficiency, reduce setup times, and expand the scope of achievable geometries in machining processes.
What are some real-world examples of parts produced using CNC milling and CNC turning?
CNC turning is commonly used to manufacture cylindrical components like bushings, rings, shafts, and flanges, while CNC milling is preferred for crafting complex engine components, custom gears, aerospace parts, enclosures, customized tooling, and prototypes of consumer products.
How can I optimize the selection and execution of CNC milling and CNC turning processes for my projects?
This requires a comprehensive understanding of part requirements, material properties, machining capabilities, and production constraints. Collaborating with experienced CNC machining service providers or utilizing advanced machining platforms can help streamline process selection and execution. Platforms like Komacut offer access to advanced CNC machining services, including milling and turning, along with expertise in optimizing machining processes to meet specific project needs effectively.
Related Articles
Sheet metal fabrication takes thin, flat, and bendable sheets of different types of metal and cuts, bends, and assembles them into a variety of products...
The sheet metal used in fabrication includes a very broad list of possible materials. Making the best choice for your product includes decisions about the
Product designs begin with CAD files and in order to get the parts or products you desire; those CAD files should follow specific design requirements. Placing a bend too close to a hole for example can result in fractures or deformed pieces during sheet metal fabrication.